
Sign In
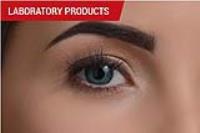
How a customised autoclave helped a contact lens manufacturer to solve a packaging problem.
Contact lenses have been used for eyesight correction for over a century. Actually it was Leonardo da Vinci who first illustrated the concept but, like so many of his ideas, the technology wasn’t available to produce them at the time. Although it is hotly debated to whom the credit belongs, the first contact lenses manufactured from glass, and fitted to cover the entire eye were manufactured in the late 1880s. Glass has obvious shortcomings including discomfort and susceptibility to damage and, by 1939, lenses were being manufactured from polymethyl methacrylate (‘Perspex’). These ‘hard lenses’ were large and, because the material does not allow oxygen to pass through, could only be worn for short periods. In 1948, English optical technician Kevin Touhy demonstrated the first corneal lenses. Smaller, lighter and more comfortable, they set the standard for future lens development. The advent of oxygen-permeable plastics in the 1960s allowed contact lenses to be worn for longer periods and comfort was further improved in the 1970s by the development of ‘soft’ hydrogel lenses which are hydrophilic and help to keep the eye moist. In the 1990s the development of silicone hydrogels with high oxygen permeability meant that these lenses could be worn overnight. But it is only relatively recently that disposable toric lenses for astigmatism have been possible.
Astigmatism is a condition in which the front surface of the eye is oval rather than the normal spherical – more like a rugby ball than a football. This changes the path of light so that the image formed at the back of the eye is not sharply focused, resulting in blurry vision, distortion of near or far-away objects and headaches when trying to focus. The lenses needed to correct astigmatism are toric, that is they have different optical power and focal length in two orientations perpendicular to each other. One of the lens surfaces is shaped like a section through a torus and the other one is usually spherical. Such a lens behaves like a combination of a spherical lens and a cylindrical lens. People with astigmatism may also share other eye defects with other lens users. These might include myopia or hyperopia, which require correction, but also scarring, complete lack of iris, double vision, divergency or similar defects of one eye which require a tinted, cosmetic or prosthetic lens to match their good eye.
PolyDev, based in Dunleer, Co Louth, Ireland, is a leading manufacturer of low volume, high value toric cosmetic contact lenses, bringing together art and technology to support the aesthetic needs of contact lens wearers. TORIColors is a monthly replacement Cosmetic Toric Lens available in a range of colours and is the only moulded cosmetic lens with astigmatism correction. PolyDev also manufactures normal spherical lenses for myopia and hyperopia and plano lenses, with no correction, for those with a requirement to change their eye colour. PolyDev’s lenses are manufactured from ‘Extreme H2O 54’ a non-ionic, glycidyl methacrylate-hydroxyethyl methacrylate (GMA/HEMA) copolymer with a high oxygen permeability of 21 Dk. For those unfamiliar with this unit, D is the diffusivity of oxygen through the material (cm2/s) and k is the solubility of oxygen in the material multiplied by the pressure (ml O2/ml of material x mm Hg). TORIColors lenses are approved for sale in the US, which means that the production facility in Dunleer has to meet the demanding standards of the US Food and Drugs Administration (FDA).
Contact lenses have to be sterilised prior to packaging, and PolyDev use a 120 litre front opening Swiftlock autoclave. Most small volume contact lens processors package their lenses in vials containing a saline solution with added wetting agents, PolyDev package theirs in the more convenient blister packs. However, this sets some challenges when it comes to carrying out the safe sterilisation of the sealed contact lens blister packs prior to distribution. “It means that sterilisation has to be done in a carefully pressure-equalised manner as the temperature is raised, maintained and lowered in the autoclave chamber,” said PolyDev’s Dr John Mulvihill, “Too much pressure and temperature applied too quickly could result in the delicate blister packs bursting or distorting. The steriliser controls the process in a superb manner.”
To achieve this result, and to meet the exacting requirements specified by PolyDev, Astell modified one of their standard autoclaves which is often undertaken to fulfil rigorous and changing requirements as scientific applications differ. The standard ‘316L-grade stainless steel’ circular steriliser chamber was complemented with all-stainless-steel orbitally welded pipework, hygienic connections, and a stainless steel frame and panelwork to suit the manufacturing environment. The pressure vessel was fitted with a heating and cooling jacket system, along with a specially designed internal fan situated inside the chamber to maintain a constant steam/air mix throughout the heating and sterilisation phases.
This had the added advantage significantly reducing cooling times. Finally, the autoclave also included an integrated all-stainless-steel steam generator for fast, controlled steam production.
Astell and PolyDev worked closely together to develop specially customised software for the steriliser’s standard touchscreen controller. This provides sterilisation programmes able to meet the requirements of a fully loaded chamber of liquid filled blister packs. This means a ramped steam/air heating to avoid bursting the sealed packs, followed by a progressive controlled ramped cooling phase after sterilisation to prevent any distortion of the product through sudden temperature change.
“We chose Astell because they were willing to discuss and agree a user specification for a smaller unit than would be the norm with highly exacting requirements. The autoclave is reliable and consistent, as would be expected for a regulated, medical device production item, and the quality of the build is excellent,” said John.
For more information on Autoclave Case Study featured by International Labmate talk to Astell Scientific Ltd
Enquire Now
List your company on FindTheNeedle.