
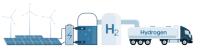
Because of the effects of carbon emissions on global climate change it is imperative that we start to think about a carbon limited future, one where alternative energy sources will be required to supplement the carbon-intensive sources that currently power our daily lives. Natural gas is available, but the supply is limited, and its costs are expected to rise because of increased demand. One promising solution to this problem is the direct use of renewably generated hydrogen in fuel cells or in internal combustion engines for transportation and electricity generation.
Although the most common element in the universe, Hydrogen isn’t found in its purest form and must be either electrolysed from water or the primary method of manufacture; stripping out of natural gas by means of steam methane reforming. Both are energy intensive processes that result in greenhouse gas emissions. Using electricity in the electrolysis process splits water into hydrogen and oxygen. The hydrogen is then removed, transported and used elsewhere to power homes, industrial vehicles, agriculture etc… the future possibilities of hydrogen are endless. So what about wind to hydrogen production and what is green hydrogen?
Key Fact: The Global demand for hydrogen is 75 million tonnes and is likely to rise sharply.
How do Wind Turbines Contribute to Hydrogen Production?
Green hydrogen starts with wind. Lots of wind. Harvesting wind offshore on a massive scale can produce stable green hydrogen on a large scale and quickly. By combining wind turbines to hydrogen production there is a synergy that reduces the drawbacks of how energy intense the electrolysis process is. A substantial proportion of offshore wind farms could eventually make hydrogen rather than transmit electricity. Safe hydrogen exhaust will be a key factor in designing these emerging renewable electrolysis technologies. Electrolysis Hydrogen ions are pulled to the cathode and Oxygen ions to the anode For wind to hydrogen generation, these systems work by linking wind turbines to electrolysers which pass the wind generated electricity through water to split the liquid ions into hydrogen (to the cathode) and oxygen (to the anode).
The hydrogen can then be stored and used later to generate electricity. The only by-product of producing hydrogen is water. Currently wind turbines produce huge amounts of energy with much of that volume going to waste as the grid cannot use it fast enough. In wind to hydrogen initiatives this energy produced from wind farms would be used efficiently to produce hydrogen, meaning none of the electricity produced would go to waste. Current developments are allowing researchers to compare different type of electrolysers and work on increasing the efficiency of wind to hydrogen systems. When a wind turbine is co-located with the electrolysis system, more direct connection between the source and the electrolyser stack is possible, this eliminates the need for long distance cables and transportation, resulting in a much more cost effective and efficient system.
The technology has the potential to deliver a completely emission free, climate-friendly method of making, storing and using energy in the future. As wind turbines are placed further out to sea, hydrogen production close to source is now even more attractive. Learn more about industrial fan types for wind turbines here.
What is Green Hydrogen?
Green hydrogen is created when hydrogen is generated without any greenhouse gas emissions. This can happen if the electrolysers that split water into hydrogen and oxygen are powered by renewable sources. Today, the world produces 75 million tonnes of hydrogen each year, most of it generated from fossil fuels, mainly natural gas and coal resulting in 830 million tonnes of carbon dioxide being released each year. Producing hydrogen with green energy will substantially reduce emissions. To enable greater use of renewable energy sources, hydrogen production from renewable electrolysis must be cost competitive.
Electrolyser manufacturers are improving and reducing the capital cost of electrolyser systems and more work is being done to optimise and improve the performance of the the power source, interfacing power electronics and other components to lower costs. Fan Integration into Wind to Hydrogen Technologies Hydrogen is a IIC gas and belongs to the T1 temperature class, making it one of the hottest and most dangerous gases. When mixed with oxygen hydrogen is a highly explosive substance that is odourless, colourless and lighter than air. The lightweight element accumulates above the oxygen and where effective ventilation is not in place, a build up can occur. In extreme circumstances there have been explosions where the build up of hydrogen has caused huge factory explosions. A small smoulder can create a huge explosion when hydrogen is in the presence of oxygen.
Industrial Fans for Wind Turbines
Aside from hydrogen exhaust, industrial fans are used across various functions of a wind turbine as described below:
Generator Cooling
Cooling is needed for the the safe operation, longevity and efficiency of the work horse of the wind turbine; the generator. The generator acts as the core and undertakes the process of turning the movement (the kinetic energy) into electrical energy. Obviously during this process heat is generated.
Transformer Cooling
Extract fans help to dissipated the heat generated in the winding of dry transformers to ensure they are spread over the surface of the coil. Fans are used to simultaneously spread the ambient air to cool down the transformer.
The following advantages result from efficient transformer cooling:
- Higher peak loads can be achieved
- Improved energy efficiency
- Increases the power of the transformer
- Longer life due to the constant distribution of temperature
Inverter Cooling & Cabinet Ventilation
Inverters are required to ensure that the generated current can be injected into the grid at a constant voltage and frequency. For cooling the inverter and sensitive electronic components, fans can be roof mounted or extract from the sides of the enclosures. This can be achieved with a combination of filter fans and exhausts or GKH and DKH fans for higher airflows.
Ventilating the Tower & Nacelle
Depending on the construction of the turbine, the fan types suited to ventilation in the tower and nacelle areas are centrifugal plug fans or axial fans.
Is an ATEX Fan Always Required for Wind to Hydrogen Systems?
Most wind to hydrogen systems will incorporate combustible gas (CG) detectors that monitors the air flow from the generation cabinet and the compression building air make up and will shut the system down if a set % of the lower flammability limit of hydrogen in the air is reached. The lower flammability limit of hydrogen in air is 4% by volume. Typically an exhaust fan installed in the production and compression building would run continuously during production to avoid a potential build up of the combustible hydrogen gas. A differential pressure switch on an exhaust fan that indicates proper airflow can be used to inhibit the operation or the electrolyser and compressor to ensure safe working conditions at all times. Pressure switches are monitored by the programmable logic controller (PLC) so the system is always monitored effectively. An ATEX fan would be required if it was situated in the air that contains the hydrogen gas. Cooling fans are also required for various system components for optimal performance and to prevent overheating and fans may be used to continuously purge the building for safety.
One of the largest consumers of ancillary power may very well be the fan that continually forces fresh air through a generation cabinet. As fan integration experts we receive a lot of enquiries around hydrogen exhaust for gas group IIC or IIB + hydrogen. In many instances it is necessary to integrate an ATEX fan whilst in some systems we can advise of methods of integrating an alternative fan and avoiding the requirement for ATEX certified industrial fan components. Our application knowledge covers a vast range of renewable technology systems including those of renewable energy generation such as wind farms. You can trust that Axair fans will supply the right industrial fan for your requirements. Axair's range of ATEX certified fans are suitable for IIC gas groups for the safe and effective removal of hydrogen gas.
The National Renewable Energy Laboratory - Wind to Hydrogen Project Case Study
Xcel Energy and the US Department of Energy’s National Renewable Energy Laboratory collaborated to design, install and operate one of the first Wind to Hydrogen projects. As the largest provider of wind generated electricity in the United States, Xcel Energy worked with the NREL to establish and understand state of the art renewable electrolysis equipment and the operation of a renewable hydrogen production facility. The system was approved for initial operation in 2007 and enjoyed success as a demonstration project, producing hydrogen directly from renewable energy sources. Across the Wind2HW systems, many systems were integrated to safely produce, compress, store and use the hydrogen gas with the heart of the system being three hydrogen producing electrolysers.
Need Help with Wind to Hydrogen Fans?, Ask us anything, we understand your application and we’re here to support you when you need us. Call us on 01782 349340.
For more information on Industrial Fans for Wind to Hydrogen Renewable Energy Generation talk to Axair Fans UK Ltd