
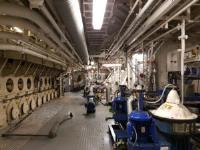
There are two situations that can greatly reduce an engines life and efficiency; the use of dirty fuel and more relevant to this article, inadequate engine room ventilation and ventilation of engine components. In short, engines that ingest cool air burn more efficiently than those that ingest warm air.
Engines produce a lot of heat, that’s how they operate and how they produce power. They must be adequately cooled to provide ample ventilation for continued operation. The warmer an engine room is, the harder it is on the components and systems housed there; heat encourages accelerated aging, higher failure rates, and greater operating expense due to the system working less efficient. In addition to this, and of importance to both builders and end users, the failure to meet engine manufacturer temperature guidelines can result in denial of warranty coverage for the engine or generator.
All but the smallest engine and engine room installations will almost certainly require some form of mechanical ventilation. Centrifugal fans rated for continuous duty are the most common type of industrial fan used to fulfil this requirement.
Why Is There A Need For Engine Room Ventilation?
Engine room ventilation falls into two categories, those required for cooling the space, and those needed for combustion. The air used to cool the compartment improves not only the combustion efficiency, but also the longevity and efficiency of gear in this space, including engines, generators, compressors, and electrical and electronic components, this also makes it a more comfortable place to work for ship employees.
Additionally, heat takes a toll on other components such as generator couplings, belts, motor mounts, as well as batteries. Whenever possible, it’s always preferable to locate batteries, particularly the house bank, outside engine compartments. This is an area that needs to be considered when on board as 24V DC power supplies and ATEX requirements in some instances will influence the choice of industrial fan suitable.
Depending on the engine room size and space available for ducts, mechanical ventilation frequently is required to achieve engine manufacturer requirements. Mechanical ventilation should include both inlet, known as supply air, and exhaust air. In the ideal installation, supply air will be ducted into the engine room low, near the interior floors, and away from heat sources, while exhaust air will be drawn from the top of the space, directly over heat producers such as engines. Duct designs should, however, avoid blowing inlet air directly onto engines in that this causes cool air to rapidly heat and be dispersed around the compartment.
In many occurrences, high inlet and high exhaust ventilation arrangement is among the least efficient. One ideal set up is to position high capacity axial fans, to insert both combustion air and cooling air alongside smaller exhaust fans which can be used to pull cooling air only. As an engine room heats up, the exhaust fans duty increases and the resulting depression ramps up the intake fans. Many boats were built previously without adequate engine room ventilation but this should be considered of paramount importance in vessel design and build.
For more information on Marine Environments talk to Axair Fans UK Ltd