
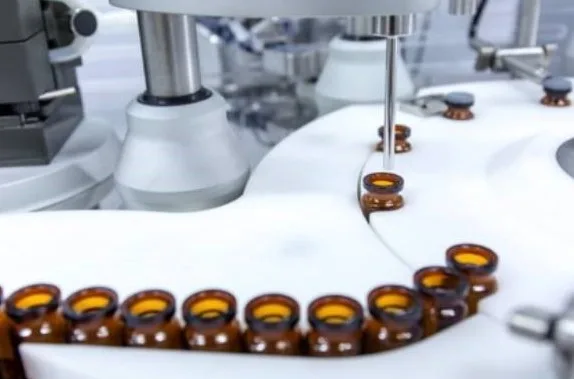
The pharmaceutical industry thrives on innovation, and it's the careful orchestration of science and manufacturing expertise that ultimately delivers life-saving medications to patients. A crucial link in this chain is aseptic fill-finish, the process of sterilely filling and sealing vials, syringes, or cartridges with injectable drugs.
In the realm of pharmaceutical manufacturing, few steps hold more importance than aseptic fill-finish. This critical process safeguards the efficacy and integrity of sterile medications, ultimately ensuring patient safety and regulatory compliance. The pharmaceutical industry is experiencing a surge in demand for aseptic fill-finish processing lines and equipment. This trend is driven by the increasing prevalence of injectable drugs, the need for enhanced product safety, efficacy, and stricter regulatory compliance requirements.
In the UK and Ireland alone, the aseptic fill-finish market is poised for significant growth; it is projected to reach ~£3.8 billion (approximately €4.4 billion) by 2025, up from ~£2.4 billion (approximately €2.8 billion) in 2022. This rise reflects the growing recognition of the critical role fill-finish technology plays in ensuring patient safety and optimizing drug delivery, making a closer look at its burgeoning trend timely. In recent years, this critical step has witnessed a surge in the adoption of specialized processing lines and equipment, driven by a convergence of factors:
Precision Under the Microscope: Why Equipment Matters
While rigorous scientific research and development are crucial for drug development, successful injectable production hinges on choosing the right aseptic fill-finish equipment. Injectable products bypass the body's natural defences, making sterility paramount. Improperly designed or operated equipment can introduce contamination, leading to potentially life-threatening infections for patients.
Beyond sterility, precise dosing accuracy is another critical factor. Underfilling or overfilling vials, syringes, or cartridges can compromise the therapeutic efficacy of the drug, leading to suboptimal or even harmful outcomes for patients.
Navigating the Regulatory Landscape: Compliance and Quality Assurance
Pharmaceutical companies producing injectable drugs must adhere to stringent regulations that govern injectable drug production. Aseptic fill-finish systems designed with compliance in mind offer features like:
- Validated cleaning protocols: Easy-to-clean equipment surfaces, and automated cleaning cycles ensure thorough decontamination between batches, upholding regulatory standards.
- Data integrity and traceability systems: These systems document and track every step of the process, facilitating audits and ensuring product accountability.
- Container closure integrity testing: Automated systems verify the seal strength and integrity of vials and closures, preventing contamination and product leakage.
Patient safety reigns supreme; sterility, therefore, becomes an absolute necessity. Modern aseptic fill-finish systems prioritize this imperative through features like:
- Integrated cleanroom environments: Isolators and Restricted Access Barrier Systems (RABS) create enclosed, sterile zones for filling and sealing, minimizing the risk of contamination.
- Advanced sterilization technologies: Tunnels, washers, and depyrogenation ovens employ validated methods to eliminate microorganisms and pyrogens, preventing patient infections and febrile reactions.
- Automated inspection systems: In-line cameras and leak detectors meticulously inspect vials and closures, ensuring only pristine containers reach patients.
Biopharma Group: Partnering for Aseptic Excellence
Through its partnership with ATS Scientific Life Sciences, Biopharma Group provides a comprehensive range of aseptic fill-finish equipment tailored to the specific needs of injectable product manufacturers in the UK, Ireland, and France. Their focus is on delivering systems that meet the highest standards of sterility, precision, and regulatory compliance, by identifying the correct system and configuration that best suits your production requirements.
Case Study: A Customer Success Story
The benefits of investing in cutting-edge aseptic fill-finish solutions are multi-faceted. A leading pharmaceutical company manufacturing a “blockbuster” drug, facing production issues with outdated equipment causing batch release delays, approached and partnered with Biopharma Group to invest in an ATS aseptic fill-finish unit specifically designed for sterile processes. The results were very impressive:
- 50% reduction in waste product
- 20% increase in production efficiency
- 30% reduction in downtime
- Significant improvement in product quality observed
- Clear return on investment
This case study exemplifies the transformative potential of Biopharma Group's aseptic fill-finish solutions. By optimizing processes and ensuring sterility and precision, companies can enhance product quality, improve production efficiency, and ultimately, deliver safer, more effective medications to patients.
Beyond Fill-Finish: Optimizing the Lyophilization Process
For drugs requiring lyophilization ("freeze drying"), choosing the right equipment and processes is equally crucial. Biopharma Group offers a comprehensive range of freeze dryers and associated technologies, including automated loading/unloading systems and PAT (Process Analytical Technology) tools to monitor product performance throughout the drying cycle. These solutions ensure aseptic conditions and optimal product quality throughout the lyophilization process.
35 Years of Expertise: Partnering for Success
With 35 years of experience in the UK and Irish markets, Biopharma Group is a trusted partner for pharmaceutical companies seeking to excel in aseptic fill-finish and lyophilization. We understand the critical role this stage plays in ensuring patient safety and drug effectiveness, and offer a comprehensive portfolio of solutions, including:
- Aseptic fill-finish equipment: From isolators and RABS to filling lines and inspection systems, we provide a range of equipment to suit your specific needs and budget.
- Freeze dryers and lyo services: Our expertise extends to lyophilization, offering freeze dryers with advanced features and validated processes to ensure product stability.
- Technical support and training: Our team of experienced specialists provides comprehensive support throughout the entire process, from equipment selection to installation and ongoing maintenance.
Contact us today to learn how Biopharma Group can help enhance precision and sterility in your aseptic fill-finish process and manufacturing to elevate your injectable drug production to the next level.
For more information on Aseptic Fill-Finish: The Rising Trend of Precision and Sterility in Pharma Manufacturing talk to Biopharma Group