
Sign In
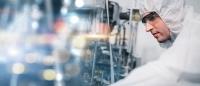
Efficient Cleanroom Performance and Safety: Why Choosing the Correct Equipment is as Important as Validation, Containment & Servicing
Cleanrooms must be regularly tested to meet regulatory specific criteria to ensure they comply with strict industry, national, and international standards. As an example, airborne particle concentrations should be tested at least twice a year for ISO Class 5 or lower, whereas facilities rated higher than ISO Class 5, need to be tested at least once a year and can be conducted as part of scheduled visits or maintenance programs and protocols. In addition, to maintain aseptic Grade A or ISO Class 5 conditions for manufacture, it is essential all products are processed and produced utilising the correct/compliant equipment.
It is highly important to follow the strict standards and keep up with validation. This is because improper care and/or use, can lead to knock-on problematic effects that can cause or lead to functionality issues such as, putting users health in the danger, or the product being worked on, being jeopardized by the introduction of unwanted particles and contaminants. The result of such occurrences being increased costs, decrease productivity, reduce staff welfare and production down-time; or worse.
Manufacturing companies in the pharma and biotech industries, along with the end-users, need reliable and effective end-to-end solutions within the aseptic fill/finish, freeze drying, and high-pressure homogenisation equipment sectors, especially for processing cytotoxic materials as well as non-cytotoxic samples that need to be prepared and processed within cleanroom or clean air environments. Biopharma Group can offer a range of quality systems following consultation, to meet your particular process requirements, such as:
Microbiological Safety Cabinets (MSCs) Class I, II, and III
For upstream processing of samples that may be used for injectable product manufacture.
oRABS / cRABS / Isolators
Aseptic vial washing and de-pyrogenation tunnels
Aseptic liquid filling, stoppering, capping machines
GMP freeze dryers with full PAT tools and automated loading / unloading solutions
GMP high pressure homogenisers.
Further to helping you find the right equipment to comply with specific legislative safety and processing standards, you benefit from access to fully trained and qualified in-house technical service engineers to look after your equipment for its lifetime. Additionally, our preferred cleanroom servicing, maintenance, containment and validation partner, Crowthorne Group, can look after all your compliance requirements from a cleanroom and containment facility perspective.
Biopharma Group is dedicated to providing the highest possible standard of service, support and products. Our goal is to ensure clients are offered experience for cleanroom equipment, maintenance plus validation. As well as helping our customers in the UK we also have, BPS Crowthorne in Ireland to cover independent, unbiased cleanroom, containment and clean air environment servicing and maintenance needs. Fully trained and CTCB-I certification qualified regionally based technical service engineers are located throughout Ireland to help you with all your Cleanroom needs from cleanrooms for small hospital pharmacies through to ISO class 1, large-scale pharmaceutical production cleanrooms. Our advice is backed by following and conforming to current Good Manufacturing Practice (cGMP), ISO 9001 and ISO 14644:2015.
In conclusion, it is clear to see that without proper validation, servicing and equipment a cleanroom may not be working at its best, or might not meet legislative standards. Biopharma Group can support you through every stage of the process with specialists who have the years of experience to back it up. Reduce costs, increase workflow and eliminate stress with Biopharma Group.
For more information on Efficient Cleanroom Performance and Safety: Why Choosing the Correct Equipment is as Important as Validation, Containment & Servicing talk to Biopharma Group
Enquire Now
More News
List your company on FindTheNeedle.