
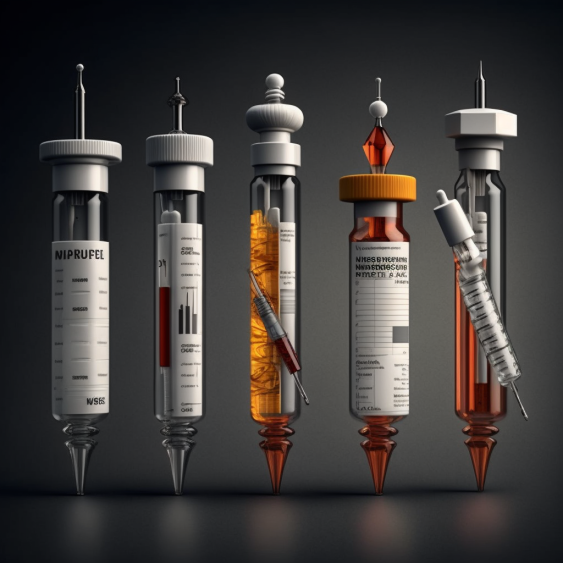
Handling potent ingredients in pharmaceutical and chemical treatments, especially in the production of precision medicines, requires stringent measures to ensure the safety of workers and the quality of the pharmaceutical products. For such applications, a cytotoxic isolator can protect both the operator and the surrounding environment from exposure to toxic active agents, and here’s how they achieve it:
- Containment and Isolation: Gloveboxes and containment systems are designed to provide a sealed and controlled environment. They prevent the escape of potent substances into the surrounding atmosphere, minimising the risk of exposure to personnel and maintaining a clean workspace.
- Operator Protection: These systems typically incorporate high-performance filtration systems and advanced glove technologies to protect operators from exposure to hazardous materials. This is crucial when working with HPAPIs (high potency active pharmaceutical ingredients), as even trace amounts can be harmful.
- Product Integrity: A cytotoxic isolator can offer a controlled environment to handle and process HPAPIs without compromising the integrity of the pharmaceutical product. This is particularly important for precision medicine production, where the accuracy of dosage and formulation is critical.
- Ease of Operation: These systems are designed to be user-friendly, allowing operators to perform tasks with precision and efficiency. This is essential in pharmaceutical manufacturing, where accuracy and repeatability are paramount.
- Regulatory Compliance: Using specialised equipment for handling HPAPIs ensures compliance with stringent regulatory requirements for the pharmaceutical industry, including those related to worker safety and product quality.
Cytotoxic isolators operate by drawing ambient air through H14 filters at the inlet, located on the transfer hatches, with an inlet HEPA filter. This creates laminar flow conditions within the hatches. The air then undergoes an additional filtration step at the back of the hatches before being drawn into the recirculating channel behind the working chamber.
Pressurised air is directed into the plenum and then downward into the working chamber to safeguard the handled products and prevent cross-contamination. The entire volume of sterile air is forced through front and back slots of the work surface, reaching the main H14 HEPA filter beneath the work surface. Afterward, the air is recirculated from the duct channel behind the rear panel, where it mixes with air from the transfer hatches.
A portion of the air is exhausted after passing through H14 HEPA filters, while another portion is recirculated back into the working chamber.
The GloveFAST Cyto Pharma manufactured by Faster S.r.l meets these needs with standard features like a soft-touch control panel, containment through gloves and sleeves, AISI 316L work surfaces, as well as interlock hinged tempered glass doors.
The frontal window made from stratified glass has gas springs for safe cleaning and closure, and along with the transfer hatches, and exhaust filters is equipped with additional safety measures, including electromagnetic interlocking systems and provision for decontamination processes.
The GloveFAST Cyto Pharma units have received TUV certification, meeting international standards such as ISO 14644-1, ISO 14644-7, and ISO 10648-2.
Test results demonstrate that the isolator is classified in Class 3 with a low hourly leak rate, ensuring a high level of containment. It is designed for safe, aseptic preparation and handling of hazardous materials cytotoxic drugs, manipulation of antineoplastic chemo-therapeutics and CMR, and to provide an EC GMP Grade A clean air environment in laminar flow conditions, isolating the operator and the environment from the process and its constituent parts.
It is important to note that the effectiveness of such equipment depends on various factors, including the design of the system, the quality of materials used, and adherence to proper operating procedures. Before implementing any equipment, thorough validation and testing must be conducted to ensure its suitability for the specific processes involved in the production of targeted cancer therapies which, as the exclusive distributor to mainland UK, Biopharma Group’s airflow products specialists can help with.
For more information on How do cyto pharma isolators keep products and operators safe? talk to Biopharma Group