
Sign In
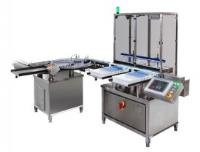
Contemporary procedures to ensure cleanliness of vials, for use in aseptic processing environments, appear to be at the forefront of technology more than ever before.
This may, in part, be associated with increased attention from regulatory agencies, and the drive towards compliance as a result. The presence of micro-organisms and other contaminants can have severe consequences, for example, should foreign material enter the bloodstream, following administration of an injectable drug product.
Manually washing vials can be cumbersome and inefficient, with large variations in the level of cleanliness batch to batch and vial to the vial; an inconsistency which poses issues during validation. Proper and thorough vial washing, depyrogenation, is therefore critical to ensure the safety of patients. The purchase of pre-sterilised containers, however, can be cost prohibitive as a long term solution.
Continuous aseptic processing, therefore, has significant advantages, which is why it has fast become a recommended practice within manufacturing facilities, and a popular solution to this conundrum. In less than 30 minutes, a container can move from the vial washing machine, into the sterilisation/ depyrogenation tunnel, and finally towards the filling/ stoppering/ capping machine – no operator intervention or re-contamination occurs during any point of the aforementioned cycle.
Orw500 3f course, equipment can be used in such a way that strictly adheres to any cGMP guidelines, to satisfy the strictest of process and cleaning (CIP/SIP) or software compliance (CFR 21 Part 11), too – another favourable facet of the technology.
While it is now becoming more accepted that aseptic process equipment is the way forward, it is essential to know which to choose in order to achieve the best results.
PennTech vial washers have no moving parts underneath the vial washer base plate itself, no gears, no belts, chain, grease points, to name a few with the main drive being servo-motor controlled. There are only two moving parts inside the wash chamber, the central column and the out-feed mechanism.
It is prudent at this stage to emphasise the purpose of a vial washer is to remove particulate and every moving part generates particles.
PennTech’s design as described above, meets this criterion, unlike other similar instruments which incorporate a large volume of moving parts inside the washing area, specifically increasing the risk of recontamination of cleaned vials; an occurrence that should always be avoided.
PennTech is a world leader in the field of complete aseptic vial production lines with a focus on simplicity, efficiency, and a compact footprint. Whether the use is for full cGMP compliance or not, PennTech can offer a suitable and affordable solution for your application needs.
As exclusive agents for the PennTech product range in the UK, Ireland & France, Biopharma Group is able to assist in assessing the best aseptic processing machinery for your needs including:
To read the full article please follow the link
For more information on The Rise of Low Maintenance, Automated Aseptic Processing Lines talk to Biopharma Group
Enquire Now
More News
List your company on FindTheNeedle.