The OV Group is a confectionery ingredient and decoration specialist with multiple locations across Britain, mainland Europe and Australia. OV is made up of four divisions spanning Confectionery, Ingredients, Retail and Foodservice and Dairy Supplies.
The company’s Leominster site is tasked, amongst other things, with packaging and logistics for a range of retail clients. This involves processing bulk finished products and repacking into retail pack units, which are either shipped to retailers or warehoused on behalf of customers to cope with seasonal demand.
With a large number of retail customers to supply, from national supermarket chains to local independents and a huge array of finished products, batch code labelling requirements are very extensive and production line output changes frequently.
Prior to embarking on an automation project, the company relied on hand labelling to cope with the extensive variety of labels applied, but recognised that labelling automation was the only long-term answer to the situation. This was partly driven by a need to improve efficiency, but equally to free up human resources to focus on other tasks.
Seeking a solution, Assistant Operations Manager Chris McHugh attended the 2021 Processing and Packaging Machinery Association (PPMA) show to identify a print and apply labelling system and a partner that could deliver what the business needed.
Chris McHugh takes up the story: “It was at PPMA that I became aware of Cobalt. I was specifically looking for an industrial print and apply partner and having visited the stands of all the suppliers present, I was particularly impressed with the Cobalt machines. They appeared very well built and also had a small footprint which met my criteria.”
With the introductions made, a site visit was organised to better understand the exact requirements of the project as Chris Hunt, UK Sales Director for Cobalt explains: “Following a site survey from one of our sales consultants, we were in a position to recommend an appropriate solution. In this case, that was for a pair of Nexus 20 Dual Action Print and Apply machines which are perfectly suited to the needs of this project for a number of reasons.”
“The machines accommodate two sided case print and apply labelling in a single process and in a variety of positions. This adaptability and flexibility is incredibly useful in this application due to the varying label needs of different retail environments.”
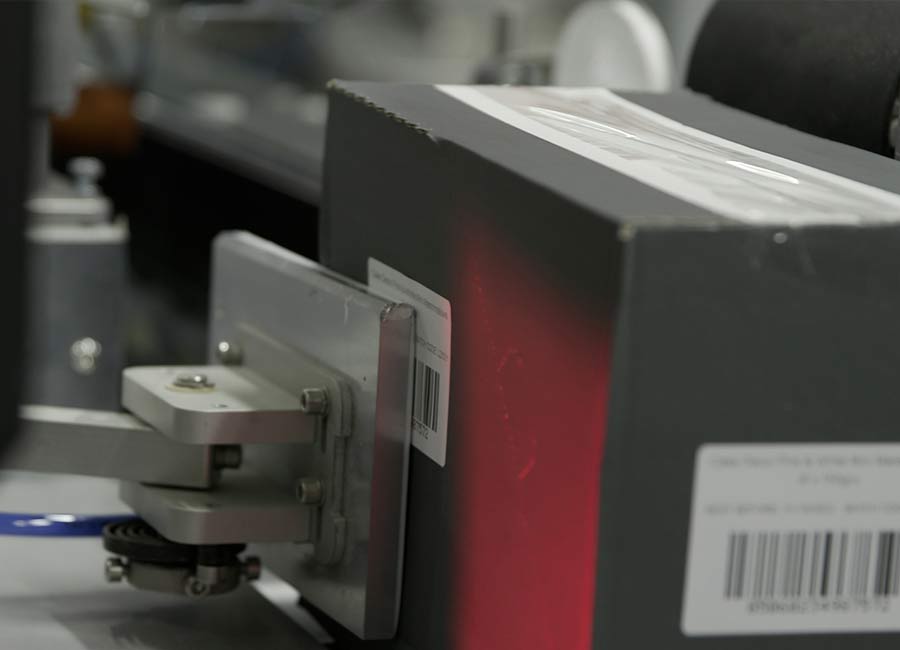
Conventionally, many have used the wraparound label approach which is troublesome and less flexible. Cobalt’s approach, which is delivered via the Nexus 20 Dual Action machine, works by independently printing and applying two labels for extra flexibility.
To handle the high volume of different labels, Microsoft Dynamics 365 ERP integrates with NiceLabel software to dynamically specify the label content which in turn allows the print and apply machine to determine if one or two labels are required and in which locations.
The system uses Cobalt Sentinel Onboard validation, which validates that the label has been successfully applied and the barcode reads to an acceptable level. For Chris McHugh, the result is just what he was looking for. “We’ve been able to improve our efficiency, become more adaptable and flexible and we’ve been able to free up staff to work on other things, which is very important when it’s harder than ever to recruit good team members.”