
Reynolds Catering Supplies
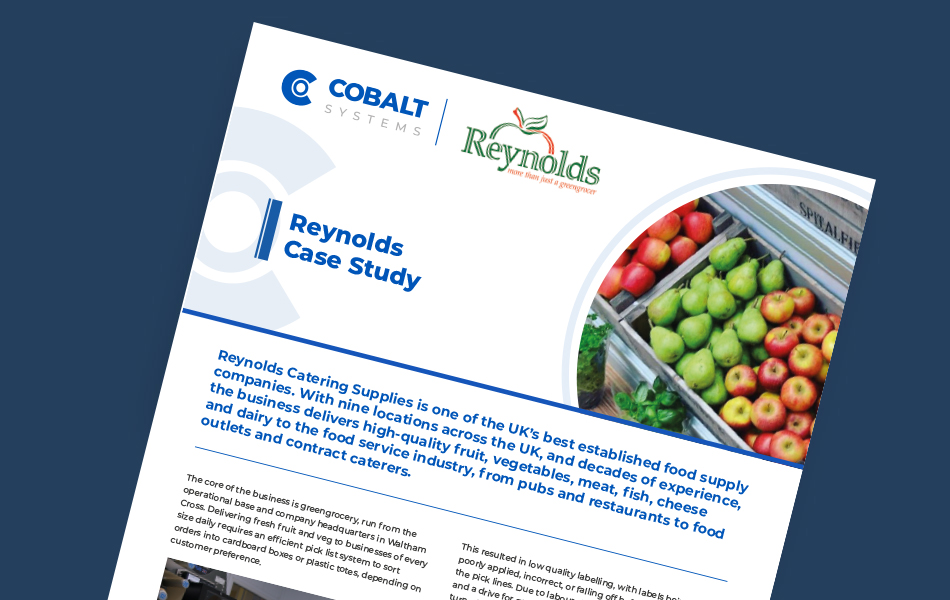
Reynolds Catering Supplies is one of the UK’s best established food supply companies.
With nine locations across the UK, and decades of experience, the business delivers high-quality fruit, vegetables, meat, fish, cheese and dairy to the food service industry, from pubs and restaurants to food outlets and contract caterers.
The core of the business is a greengrocery, run from the operational base and company headquarters in Waltham Cross. Delivering fresh fruit and veg to businesses of every size daily requires an efficient pick list system to sort orders into cardboard boxes or plastic totes, depending on customer preference.
Every day, Reynolds receives orders totaling circa 8,000 boxes and totes which need to be labelled at the start of the packaging line with pick lists that instruct staff what items needs to go in which containers.
In the past, Reynolds relied on a very manual process to print and label each tote or box by hand at the start of each shift. They used desktop printers separate from the conveyor line to print the labels before a worker would take each label and apply it manually.
In the past, Reynolds relied on a very manual process to print and label each tote or box by hand at the start of each shift. They used desktop printers separate from the conveyor line to print the labels before a worker would take each label and apply it manually.
Cobalt implemented an automatic labelling solution capable of labelling both types of container – totes and boxes – correctly each time. A single machine labels both the front face and side face as they pass along an inbuilt conveyor. This posed several challenges. The different surface materials, differing angle of applications (with boxes being flat while totes are angled) and the different weight of the boxes themselves.
These challenges are dealt with by:
- Specifying that the right media is used that can cope with both surfaces
- Using a foam applicator pad that has sufficient leeway to allow for changing angles
- Physical stops are built in to the conveyor which pop out to hold the different containers in their
respective places and ensure enough pressure can be applied
The machine is fed data from Reynold’s ERP system Infor M3. Pick lists are ordered within the ERP and sent to the print and apply machine along with instruction as to whether a box or tote is to be used. These are automatically fed onto the conveyor and a box-making machine sits ahead of the print and apply machine making up boxes in real-time as they are needed.
The team at Reynolds determined that more control over the process was needed, especially for more granular changes and for “on-the-fly” adjustments. As a result, the in-house Business Development Team developed a secondary queueing system before the labelling occurs to allow for manually sorting the totes and boxes, prioritising the items that need to be sent out first and enabling further efficiencies down the picking lines.
This combination of technologies and understanding of their operational requirements meant the Reynolds team was able to integrate Loftware NiceLabel into their ERP system to efficiently manage the queue at the beginning of the shift, creating an intuitive workflow for packing produce into the boxes and totes.
The finished system can print and apply labels on totes and boxes and label each at a speed of 23 to 26 per minute while applying the labels in the correct orientation. A second machine sits in series with the first, but is dormant – only being used if an error occurs with the first.
As a result, the capacity of Reynolds’ production lines has increased greatly, with shifts starting later and ending earlier than previously and opening up the potential for fulfilling more orders as the business continues to grow.
The changes to their labelling system – and particularly the integration of Loftware NiceLabel into their ERP system – has allowed Reynolds to reduce the number of staff needed in this part of the picking line from five to just one, allowing staff to be re-deployed elsewhere in the operation.
The changes to Reynolds’ operation also brought about savings in space on the operations floor, as well as creating a calmer, more pleasant working environment.
For more information on Reynolds Catering Supplies talk to Cobalt Systems Limited