
Sign In
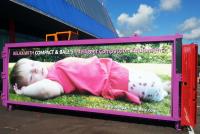
As one of Kent’s fastest growing food companies, Watts Farms has always committed to using the latest products, savings and innovations. When they discovered that they could reduce their waste management costs by 20%, increase their compactor container capacity by 20% and make mill size bales whilst achieving 20% labour cost savings with two new machines it didn’t take them long to make the switch. Caroline Ayears-Johnson, Group Technical Manager at Watts Farm is very happy to tell everyone about the new Gillard Mi3 compactor and Strautmann BalePress 53 machines that have achieved these results.
‘During a review meeting with Compact & Bale, it became clear that we had outgrown our existing waste machinery supplied in 2007. Due to considerable investment and growth in our business, the types and volumes of our waste had changed to the point where Compact & Bale were able to show us that we were losing hours of labour every week and incurring considerable unnecessary costs. They conducted a detailed review and presented a proposal to replace our old machinery with two new machines’ says Caroline.
Compact & Bale have been supplying waste compaction and baling equipment since 2000 and have worked with Watts Farm since 2007. As UK agents for Strautmann, Packmat, Ludden & Mennekes and Gillard, Compact & Bale supply the latest intelligent compaction equipment from Europe’s leading manufacturers so Caroline was keen to look at the latest products in their Automate to Save range.
Compact & Bale Director, Steve Burnett says ‘the first new machine we installed was a Gillard Mi3 portable compactor. This is the only compactor on the market that uses a patented triple cylinder that avoids all the problems and costs of the twin, cross over cylinders on traditional design machines. The triple cylinder design also gives the machine an additional 20% container capacity that translates to 20% more compacted waste carried for the same transport cost.’
In addition to the new compactor Caroline says ‘we also replaced our old baler with a new mill size machine that makes 450-500kg bales that we store and sell for a far higher rebate in maximum 24 tonne payloads. This alone has enabled us to earn at least 20% more revenue from the sale of our cardboard. Plus we have also reduced our labour costs by at least 20% as loading the new baler is so much easier and faster. It has a huge feed aperture and fast cycle time, and the bales weigh 4 times as much as the old ones so we spend less time tying, moving and stacking them and don’t buy so many ties!’
The Strautmann BalePress 53 produces wire tied bales that meet the UK mills standards and loads 24 tonnes to a trailer, minimizing haulage costs and maximizing rebates. Steve Burnett says ‘we recommended the 53 tonne press machine as Watts’ cardboard is full of tri-wall fruit box that is tough to compact in many lesser machines but being German built and weighing over 2.5 tonne, the BP53 doesn’t miss a beat.’
‘Delivery, installation, training and removal of the old machines was all handled by Compact & Bale. They know their business which lets us get on with ours. In fact, they are so good we would use them again… oh, we just did!’ says Caroline.
For more information on Watts Farm Reduces Waste Labour Costs By 20% With Gillard Mi3 Compactor talk to Compact & Bale Ltd
Enquire Now
More News
List your company on FindTheNeedle.