
Sign In
Hospital Pharmacy Isolators - The Future
01-08-2007
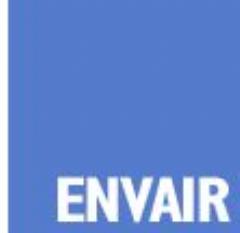
Hospital pharmacy
isolators: the future
John Neiger
Consultant
Envair Limited
Haslingden
UK
W:www.envair.co.uk
From large-scale centralised services and facilities serving a number of
hospitals to small-scale units, the development of isolators is keeping pace
with the requirements of regulation, health and safety and new standards
Hospital Pharmacy Europe September/October 2004
Sponsored profile Envair
Isolators have now been in use in UK and certain
European hospital pharmacies for over 15 years.
When isolators first appeared on the scene in the
late 1980s, they originated from three distinct sources,
reflected in the respective design solutions. The first
source related to the nuclear industry and utilised
components from that industry to develop large “sterile”
isolators. These had very low air change rates and
were gassed with peracetic acid. Materials were transferred
between “sterilising” isolators, storage isolators
and process isolators using sophisticated docking
containers. The second source related to a well-known
manufacturer of radiopharmaceutical products. Here
the focus was on radiation protection and the technology
relied on negative pressure and a turbulent
airflow. The third source related to a collaboration of
the authors clean air and containment company with
two UK hospital pharmacies. The resulting isolators
utilised the principles of unidirectional flow to ensure
an aseptic environment, with negative pressure where
operator protection was required. Transfer chambers,
purged with HEPA (high-efficiency particulate air)
filtered air, eliminated the transfer of airborne
contamination during material transfers in and out.
Developments
Gaseous sanitisation in rapid gassing ports
Hydrogen peroxide is less corrosive than peracetic
acid and breaks down into water vapour and oxygen,
which are harmless. It has therefore superseded
peracetic acid as the gaseous sanitisation agent of
choice, especially in regulated facilities. More recently,
smaller, slightly less expensive hydrogen peroxide
generators with capacities more suited to pharmaceutical
isolators than to rooms have reached the
market. But the most exciting current development is
the rapid gassing port, which replaces the isolator
entry transfer device. With a total gassing cycle time
of 15–20min, the process of gaseous sanitisation, with
all its advantages, has thus been greatly streamlined.
This should make it far more attractive in a hospital
pharmacy environment, where a speedy turnaround
of prescriptions is the normal requirement.
PLC systems
Simple PLCs (programmable logic controllers) are
now replacing the old control and instrumentation
technology. However, they offer many advantages. A
good example is the simplification of pressure decay
testing. Previously there was an SOP (standard operating
procedure), which the technician had to follow
step by step. Depending on the isolator, the PLC can
either carry out the whole process automatically from
start to finish and then report and log the result, or it
can be programmed to give operator prompts for any
manual operations. In both cases, there is no need for
a detailed SOP, and the scope for operator error is
removed. A further advantage of PLCs on isolators is
that they can be linked with PLCs on associated equipment,
such as hydrogen peroxide gas generators, to
provide overall process control and comprehensive
interlocking for safe independent use of chambers.
New standards and guidelines
This year has seen the publication of a book on pharmaceutical
isolators1 and of the final draft of ISO
14644-7.2 The former gives guidance on almost every
aspect of isolator design and use, whereas the latter
sets out basic and generic requirements for the specification
and testing of isolators. Together, they should
ensure that, as isolators continue to develop, they do
s
For more information on Hospital Pharmacy Isolators - The Future talk to Envair Ltd
Enquire Now
List your company on FindTheNeedle.