
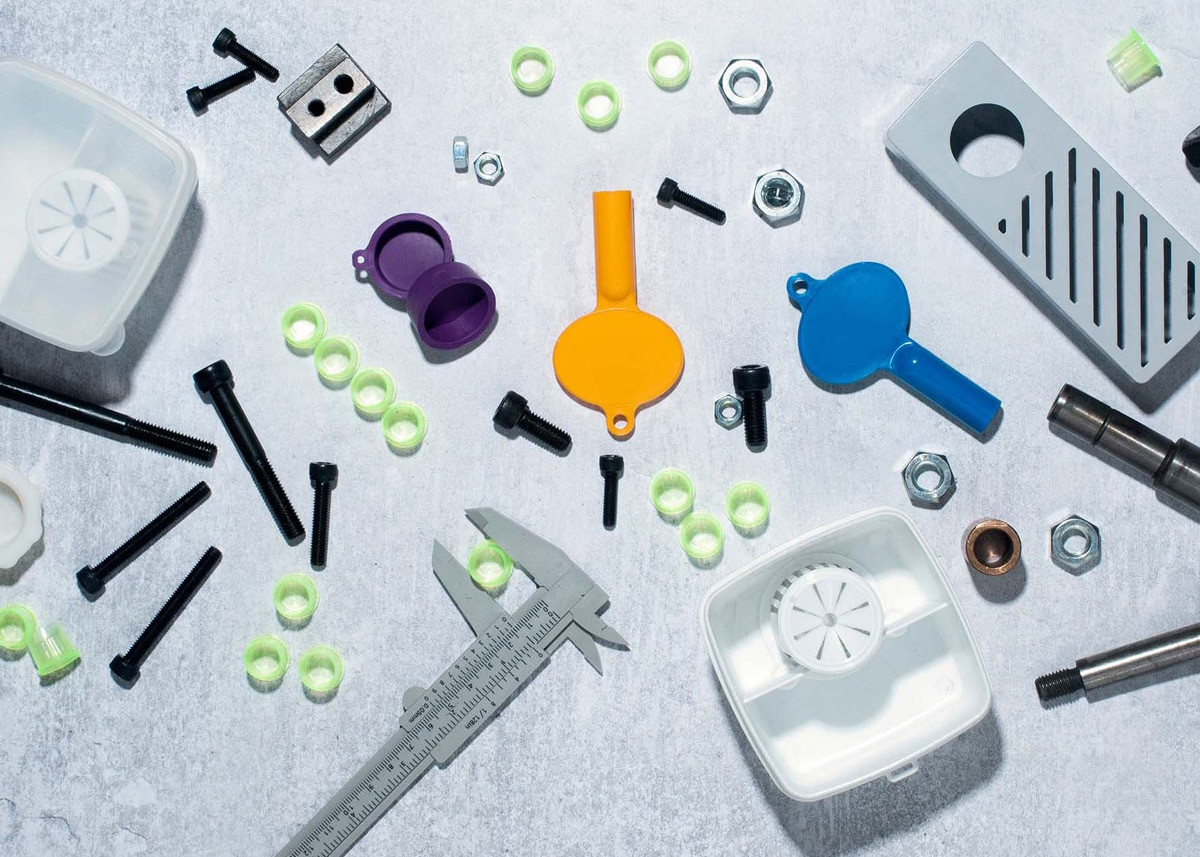
Injection moulding is one of the most versatile and widely used manufacturing processes for producing high-quality plastic components. However, like any manufacturing process, it comes with its own set of challenges. Addressing these issues effectively is key to ensuring consistent quality, minimising waste, and meeting tight production deadlines. In this blog, we’ll explore some common challenges in injection moulding and our practical solutions to overcome them.
1. Material Selection & Compatibility
One of the first hurdles in injection moulding is choosing the right material. Each component has specific requirements, whether it's strength, flexibility, heat resistance, or environmental considerations. The function of the end product must be considered, the type of environment it will be used in, and for how long. Using the wrong material can lead to part failure or production inefficiencies.
Solution:
At Great Central Plastics, we offer a wide range of thermoplastic polymers, including food-grade and engineering-grade materials. For customers prioritising sustainability, we also regularly work with eco-friendly options such as recycled, bio-based and biodegradable plastics. Partnering with an experienced injection moulder ensures you get expert guidance in selecting the right material for your needs, before the project begins.
2. Warping & Distortion
Warping occurs when parts cool unevenly, causing them to bend or twist out of shape. This issue can arise from poor mould design, uneven cooling, or unsuitable material selection. While mould tools can be modified after production, optimal tool design in the first instance will lead to best results and the most cost-effective solution.
Solution:
Optimal mould design is crucial to prevent warping of the moulded plastic products during production. Great Central Plastics provides in-house toolmaking services, allowing us to optimise moulds for even cooling and precision. Additionally, our experience in working with various materials helps minimise the risk of warping through tailored process adjustments.
3. Inconsistent Surface Finish
Inconsistent textures or surface defects such as flow lines, sink marks, or weld lines can affect both the aesthetics and functionality of a plastic product. These defects are often caused by incorrect mould temperatures, injection speeds, or material flow during the injection moulding cycle.
Solution:
Advanced moulding machinery and process controls are essential to achieving a flawless finish. At Great Central Plastics, we utilise cutting-edge equipment and techniques, including customisable finishes like pearlescent, fluorescent, and glow-in-the-dark effects, to ensure your product stands out without compromising quality. Coupled with our in-house toolroom for maintenance and tool modifications, we manage ongoing customer projects to the highest standards.
4. High Rejection Rates
Scrapped parts due to dimensional inaccuracies or cosmetic defects can significantly increase costs and waste, as well as risk damage to relationships and reputations with suppliers and customers.
Solution:
We prioritise quality at every stage of production. From in-house toolmaking to comprehensive post-moulding inspections, Great Central Plastics ensures precise manufacturing processes. Our sustainable approach also includes recycling any waste materials generated during production, helping to keep costs down while maintaining our commitment to the environment, while maintaining a high quality end product.
5. Sustainability in Manufacturing
As environmental concerns grow, companies are under increasing pressure to adopt greener practices. However, balancing sustainability with performance and cost can be challenging. Recycled materials can be more difficult to process due to fluctuations in material properties, but upcoming legislation as well as customer pressure mean that manufacturers must adopt greener and more environmentally considerated materials and processes.
Solution:
Sustainability is at the heart of what we do. We utilise recycled materials and renewable energy, with solar panels generating one-third of our energy needs. Our products are designed for durability, reducing single-use plastics and promoting a circular economy. We also have experience with moulding a wide variety of sustainable materials, from recycled, to bio-based and biodegradable, meaning we can reduce the carbon footprint of our customers products through every stage of the process.
6. Lead Times & Production Delays
Meeting tight deadlines is often a challenge, especially for custom projects requiring complex moulds, or when relying on international supply chains which are more open to unforeseen delays or quality issues.
Solution:
Great Central Plastics operates a fully automated, 24/7 production facility to handle both low and high-volume runs efficiently. By managing toolmaking and production in-house, we reduce lead times and ensure consistent quality from start to finish. With all of our products managed and manufactured entirely in the UK from our Northamptonshire facility, we’re in total control of our schedules and output, without relying on international shipping or deliveries.
Conclusion
Injection moulding challenges can seem daunting, but with the right expertise and resources, they are entirely manageable. Great Central Plastics has been delivering reliable, high-quality injection moulding solutions for over 25 years. From material selection to precision toolmaking and sustainable manufacturing, we’re here to support your project every step of the way with our knowledgeable and approachable team, from our base in Northamptonshire.
Contact us today to discuss how we can help you overcome your injection moulding challenges and bring your ideas to life.
For more information on Common Challenges in Injection Moulding & How to Overcome Them talk to Great Central Plastics Ltd