
In-House Re-Grind Facility
10-04-2025
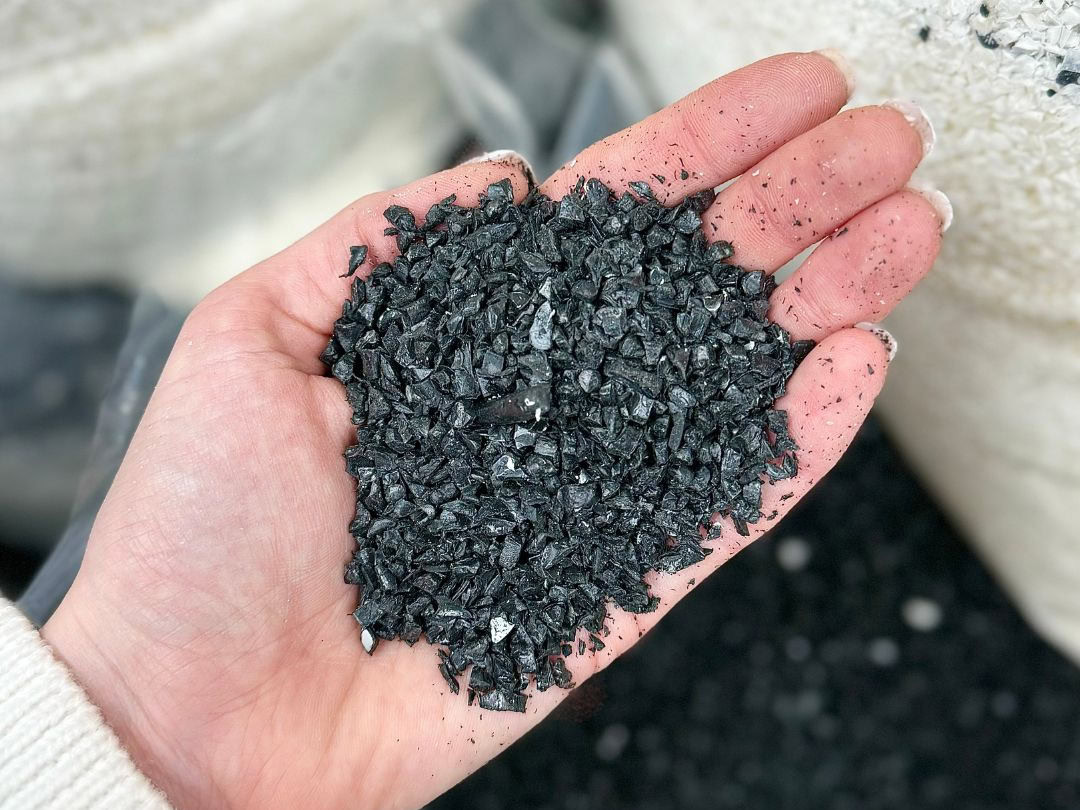
At Great Central Plastics, we take great pride in being a sustainable injection moulder, ensuring that our manufacturing processes are as environmentally responsible as possible. A key part of this commitment is our in-house re-grind facility, which allows us to re-granulate our own plastic waste and turn it back into reusable materials. By integrating eco-friendly moulding practices into our operations, we actively contribute to reducing plastic waste and promoting a circular economy.
What is the Re-Grind Process?
Re-grind refers to plastic material that has already been processed at least once and is then reclaimed by grinding it down into smaller granules. This process involves:
-
Collecting plastic waste such as rejected parts, trimmings, and sprues from the injection moulding process.
-
Cleaning and sorting the waste to remove contaminants.
-
Grinding the plastic into uniform granules that can be reintroduced into the manufacturing cycle.
By using re-grind materials, we significantly reduce the need for virgin plastics while maintaining the high-quality standards required for our products.
Our In-House Re-Grind Facility
As a leading injection moulder, we have invested in an in-house re-grind facility that allows us to take direct control over the recycling process. This means that any plastic waste generated during production is immediately collected, processed, and reintroduced into our system, ensuring minimal environmental impact.
Having this facility on-site means we can:
-
Ensure consistent quality control over re-grind materials.
-
Reduce transportation and external processing, lowering our carbon footprint.
-
Optimise material usage for maximum efficiency.
The Benefits of Re-Grinding for Eco-Friendly Moulding
Our re-grind facility provides numerous advantages, both for our business and for the environment. Some of the key benefits include:
1. Sustainability and Environmental Impact
By re-granulating our own waste, we significantly reduce the volume of plastic sent to landfill, helping to minimise environmental pollution. As a sustainable injection moulder, we are committed to reducing our carbon footprint and promoting eco-conscious manufacturing.
2. Cost Efficiency
Using re-grind materials helps to reduce our reliance on virgin plastics, resulting in cost savings that we can pass on to our customers. This allows us to provide high-quality products at competitive prices without compromising sustainability.
3. Consistent Quality Control
Since we manage the entire recycling process in-house, we can ensure that our re-grind materials meet the exact specifications required for injection moulding. This guarantees that our products maintain the strength, durability, and finish that our customers expect for their application.
4. Resource Conservation
By reintroducing re-granulated materials into our production cycle, we are conserving valuable natural resources and reducing the demand for new plastic production. This contributes to the development of a more circular economy and aligns with our mission of eco-friendly moulding.
At Great Central Plastics, our in-house re-grind facility is just one of the many ways we champion sustainability within the injection moulding industry. By transforming waste into reusable materials, we not only enhance operational efficiency but also contribute positively to environmental conservation.
We are dedicated to continuously improving our processes and investing in green technologies to ensure that we remain at the forefront of eco-friendly moulding solutions. Our commitment to sustainability reflects our belief in responsible production and our ongoing mission to support a greener future for the plastics industry.
For more information on In-House Re-Grind Facility talk to Great Central Plastics Ltd