
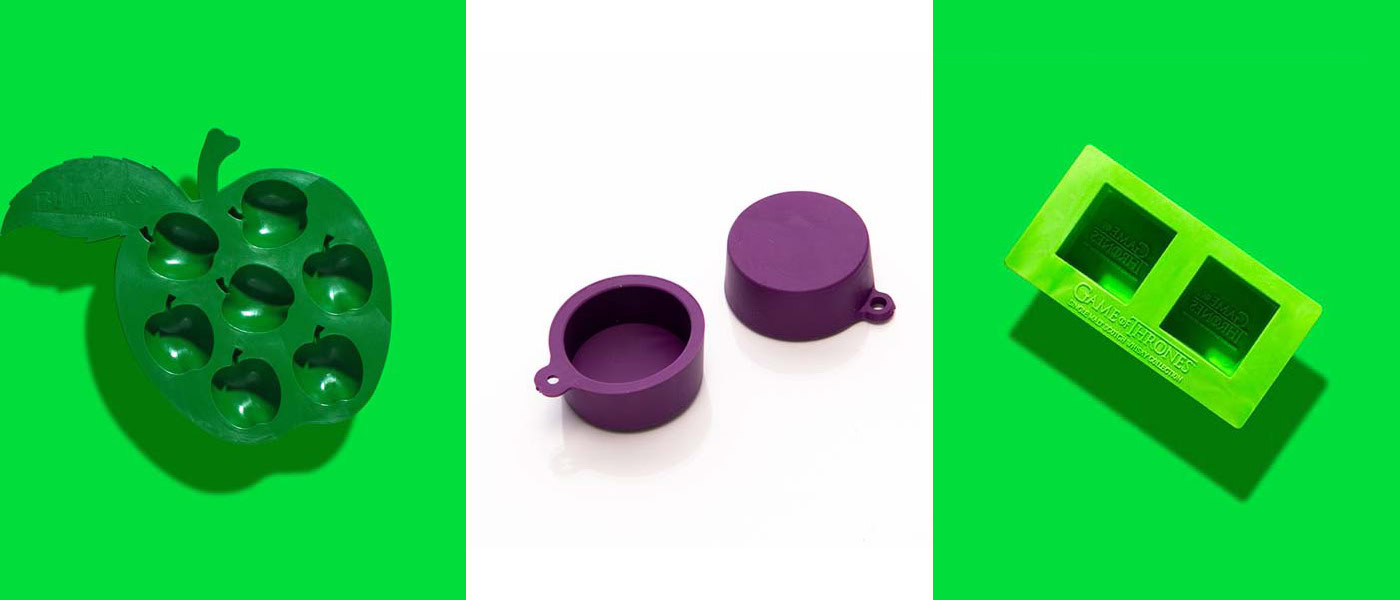
As demand for eco-friendly plastics grows, the injection moulding industry is adopting sustainable materials and waste reduction strategies to minimise environmental impact. Businesses seeking a sustainable injection moulder can now choose greener alternatives without compromising on quality.
Eco-Friendly Materials in Injection Moulding
Great Central Plastics is committed to sustainable injection moulding, offering innovative materials that help reduce plastic waste:
-
Gum-tec® – A revolutionary material made from recycled chewing gum, transforming waste into durable, mouldable plastic.
-
Bio-Flex® – A biodegradable and recyclable bio-based plastic, ideal for food-grade injection moulding and environmentally friendly packaging.
-
Recycled PPCP (Polypropylene Copolymer) – A cost-effective material derived from recycled plastic, reducing the need for virgin polymer production.
-
BDP® (Biodegradable Plastic Ingredient) – Enhances plastic biodegradability, ensuring products decompose efficiently at the end of their life cycle.
-
Waterhaul® – A premium-grade recycled plastic made from discarded fishing nets, tackling marine pollution while delivering high-performance moulding capabilities.
-
Limit X® – A versatile, food-safe plastic, available in various colours, meeting stringent sustainability and safety requirements. A limestone-based material created from the waste of the cement industry.
By integrating these eco-friendly injection moulding materials, businesses can significantly lower their environmental footprint while ensuring product quality and durability.
Waste Reduction Strategies in Injection Moulding
In addition to using sustainable materials, leading injection moulders are implementing waste reduction strategies to support green manufacturing:
1. Process Optimisation
Lean manufacturing techniques reduce excess material use and improve production efficiency, minimising waste generation in plastic injection moulding.
2. Recycling and Regrinding
Scrap plastic from the moulding process is collected, reprocessed, and reused, reducing reliance on new polymer production and promoting closed-loop recycling.
3. Energy-Efficient Machinery
Modern injection moulding machines consume less energy, lowering carbon emissions while maintaining high production efficiency. Electric injection moulders are particularly effective in reducing power consumption.
4. Biodegradable and Compostable Products
Using compostable plastics and biodegradable injection moulding materials ensures that products decompose naturally, reducing long-term environmental impact.
The Future of Sustainable Injection Moulding
With growing environmental concerns, the shift towards sustainable plastic manufacturing is essential. Forward-thinking injection moulders like Great Central Plastics are embracing innovation, ensuring that plastic injection moulding remains both efficient and environmentally responsible.
By choosing sustainable injection moulding solutions, businesses can align with consumer expectations, meet regulatory requirements, and contribute to a greener future.
For more information on Sustainable Injection Moulding: How the Industry is Going Green talk to Great Central Plastics Ltd