
Sign In
Injection Moulding or Blow Moulding?
19-07-2022
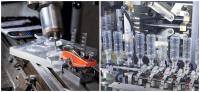
Here’s How These Two Production Processes Compare...
Deciding upon the production process for your latest product or invention can be challenging. However, choosing the correct option can be the difference between a successful product and one plagued with defects.
A common choice companies face is the one between injection moulding and blow moulding. Therefore, this brief article aims to inform you about how these two production processes compare.
Plastic Blow Moulding
Blow moulding involves forming and connecting hollow plastic parts. Consequently, it is ideal for producing bottles and other hollow products.
Advantages of Blow Moulding
There are three main advantages to using a blow moulding production process:
• Cheaper tools
• Automated process
• Mass production
Cheaper tools
Companies commonly invest in blow moulding technology because it is relatively cheap. Therefore, even if the machine malfunctions or breaks down, repair or replacement costs are inexpensive.
Automated process
Blow moulding is a completely automated process. Therefore, you can remove the risk of human error and achieve faster production.
Mass production
Blow moulding is an excellent process for mass-producing hollow products such as bottles. Indeed, defected or damaged items only occur at around a few hundred per million.
Disadvantages of Blow Moulding
Although blow moulding offers three significant advantages, it comes with several drawbacks:
• Petroleum dependent.
• Environmental impact.
• Multiple production methods required.
• Limited uses.
• Significant waste.
Petroleum Dependent
Producing a plastic product using blow moulding requires a tremendous amount of petroleum. Consequently, this reliance puts increased pressure on world oil reserves.
Environmental Impact
Blow-moulded products have a considerable environmental impact. Moreover, the use of petroleum means they are not biodegradable. Therefore, this negates the advantage of mass production as producing more increases ecological effects.
Multiple Production Methods
Blow moulding requires multiple production methods to produce the parts for more complex products. Therefore, it is more challenging to streamline the whole production process.
Limited Uses
Blow moulding hits significant challenges in producing solid products. Although it is ideal for hollow items, its reliance on air pressure makes it challenging to control wall thickness. Therefore, it has limited utility.
Significant Waste
As blow moulding is more or less restricted to hollow forms, which generates significant waste to achieve specific dimensions. Although thermoplastic stretching reduces wastage, this can result in substandard products.
Plastic Injection Moulding
Plastic injection moulding is a manufacturing process that involves molten plastic into a mould to form a part.
Advantages of Injection Moulding
Plastic injection moulding comes with significant advantages, including the following:
• Speedy and Efficient
• Flexibility of Design
• Consistency of Production
• Minimal Waste
• Low Cost
Speedy and Efficient
In the world of mass production, speed and efficiency are what make your products quality and cost-effective. With injection moulding, you can produce parts in seconds, meaning you can achieve high volume fast.
Flexibility of Design
You should not restrict your design to hollow parts or uniform colours. Injection moulding gives you increased flexibility in your design, allowing you to create complex products.
Consistency of Production
Injection moulding offers excellent consistency of production. This means you replicate every part with every turn of the machine. This result is a considerable advantage for quality control and customer satisfaction.
Minimal Waste
Reducing waste and recycling should be a huge consideration for all manufacturing companies. At Great Central Plastics, we have a robust eco-friendly ethos and minimise waste at every opportunity. Our recycling efforts include the use of recycled white goods and PPCP.
Low Cost
Plastic injection moulding is an automated process, meaning you’ll make considerable savings on labour costs. Once we've set up the production process, it runs under the control of a single operator.
Disadvantages of Injection Moulding
Of course, there are a couple of disadvantages of plastic injection moulding, such as:
• Upfront investment.
• Not ideal for low volume production.
Upfront Investment
Your product or invention is unique to you, and that is fantastic. After all, you don’t want others to copy your design or idea, right? However, to produce that unique design requires specific tools. Consequently, you need to create and test these tools, which costs money.
However, this has two upsides. Firstly, it creates a barrier for anyone wanting to copy your design. Secondly, it assures you have tools that can continue to produce quality products repeatedly. Great Central Plastics offers a tooling service and can help you reduce the costs of this requirement.
Not Ideal for Low Volume Production
Plastic injection moulding's design suits mass production. Therefore, using it for small batch production may not prove cost-effective. Of course, depending on the intricacies of your design and price point, injection moulding may be a suitable process. You can contact Great Central Plastics to find out if your project is suitable for injection moulding production.
Conclusion
The process you use to produce your product can be as important as its design. Blow moulding and plastic injection mould are two options to make your product in high volumes. This article will hopefully help you decide which one is more suitable for your product.
For more information on Injection Moulding or Blow Moulding? talk to Great Central Plastics Ltd
Enquire Now
List your company on FindTheNeedle.