
Sign In
Silicone vs TPE
01-03-2023
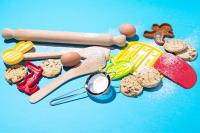
Great Central Plastics Ltd are an injection moulding company who offers TPE as an alternative to silicone-based products.
Clients often ask if we can mould their products from silicone, but in actual fact they often mean they want a product moulded in a soft flexible material. Great Central Plastics Ltd are an injection moulding company which requires hot material injected into cold tools, this is the process of moulding with thermoplastics. Silicone manufacturing is similar but involves injecting liquid silicon rubber (LSR) into hot tools. One of the thermoplastics often used when clients want a soft flexible product is TPE (Thermo Plastic Elastomer.) TPE is perfect for moulding products such as ice cube trays as it has a rubber like qualities. There a number of differences between the two processes but this article will help explain the main differences between using Silicone or TPE for your project.
From the outside, both an LSR injection moulding machine and a Thermoplastic injection moulding machine look the same. The main difference is that in Thermoplastic moulding a high pressure is required whereas in LSR moulding the clamp pressure is much lower. The reason for clamp pressure is to keep the mould tool closed whilst the material is setting / curing.
What is Liquid Silicone Rubber (LSR)?
Silicone is created by using quartz from sand. Silicone needs to be kept at a cool temperature to prevent the silicone from curing, therefore the barrel and nozzle are water-cooled during the injection process. Silicone offers great characteristics for medical-grade products due to its hypoallergenic properties.
What is Thermoplastic Elastomer (TPE)?
TPE is a polymer that is melted down from granular form into liquid when heated and solidifies when cooled. Petroleum-based TPE’s are made from fossil fuels but bio-based TPE’s are created from bio sources such as sugar cane. Great Central Plastics offers eco-friendly TPE options for products such as Terraprene. TPE has rubber-like properties and depending on the shore hardness can vary in flexibility/softness. TPE melts at high temperatures which makes it perfect for recycling as it can be reprocessed and turned into more products.
Shore hardness – a durometer scale that indicates how soft or hard a material is, a lower shore rating means the material is softer. A higher shore rating indicates the material is hard.
Choosing the best material for your project…
Due to the difference in the process of manufacturing between LSR and TPE, there is a difference in suitability for the application of the product. LSR is cured by increasing temperature and is UV stable which means that LSR is suitable for products that need to withstand high temperatures and require weather-resistant properties. Many clients in the automotive sector use LSR injection moulded products for parts that need to withstand higher temperatures. These products include gaskets, connector seals, baby bottle nipples etc.
Processing TPE is generally easier than LSR which means there are often a lot of cost savings to be made by opting to use TPE over LSR for your moulded product. TPE melts at high temperatures which means moulded products that require heat-resistant properties won’t be suitable for TPE moulding. However, this very same characteristic allows for great recyclability credentials for the material to be re-used in other products. TPE’s offer many of the same advantages as LSR with the main limitation being the heat-resistant properties. TPE can be moulded with a ‘non-tacky’ finish which is often favourable when looking to create a product that is dirt-repellent. A TPE product will stay a lot cleaner compared to a comparable LSR product. If your project doesn't require to withstand high temperatures then TPE is often the best option. Get in touch and our team will be more than happy to discuss your bespoke, eco-friendly project.
For more information on Silicone vs TPE talk to Great Central Plastics Ltd
Enquire Now
List your company on FindTheNeedle.