
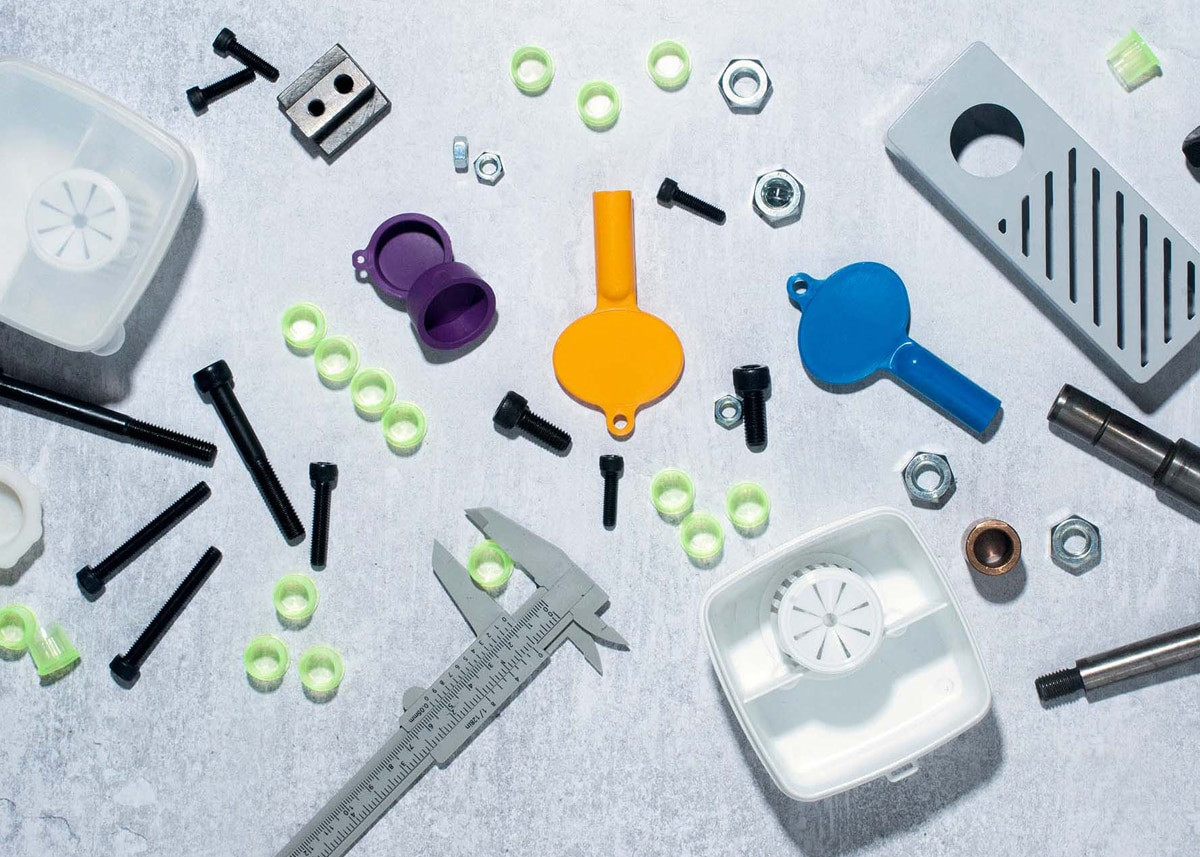
In today's competitive manufacturing landscape, ensuring the quality of products is more important than ever, especially in injection moulding, where precision and consistency are key. At Great Central Plastics, we take pride in our strict quality control measures, backed by our ISO 9001:2015 certification, to deliver reliable, high-quality injection moulded products across various industries.
Why Quality Control Matters in Injection Moulding
Injection moulding is a complex process that involves heating plastic materials, injecting them into moulds, and cooling them to form solid parts. Any variation during this process can lead to defects such as warping, weak points, or inconsistent part sizes. These issues can compromise the functionality, durability, and appearance of the final product. That’s why maintaining tight control over each stage of production is vital.
Quality control ensures that every part meets strict specifications, reducing waste and rework. It also helps to maintain consistency across production batches, which is crucial for industries such as automotive, medical devices, and food packaging, where even minor flaws can lead to significant issues.
Common Defects in Injection Moulding & How Quality Control Prevents Them
Injection moulding is a highly technical process that demands precision at every stage. When things go wrong, defects can occur, which not only waste materials but also impact the overall quality of the final product. Here are some common defects and how our rigorous quality control systems at Great Central Plastics help prevent them.
-
Warping
-
What it is: Warping occurs when different sections of the part cool at varying rates, causing the material to shrink unevenly and bend out of shape. This can result in parts that do not fit or function as intended.
-
How we prevent it: Consistent cooling is crucial to avoid warping. Our advanced injection moulding machines ensure precise control of temperature throughout the moulding and cooling stages. We also maintain uniform wall thickness in the design phase to promote even cooling and prevent internal stresses that lead to warping.
-
-
Sink Marks
-
What it is: Sink marks are depressions that appear on the surface of the part when thicker sections cool more slowly, causing them to shrink inward. This not only affects the appearance of the product but can also weaken structural integrity.
-
How we prevent it: Our design team ensures uniform wall thickness and incorporates ribs and bosses to reduce the need for thicker areas in the moulded part. During production, we closely monitor pressure and cooling times to ensure even material distribution and prevent sink marks.
-
-
Short Shots
-
What it is: A short shot happens when the molten plastic doesn't fully fill the mould, resulting in an incomplete or undersized part. This can happen due to low injection pressure, poor material flow, or blockages in the mould.
-
How we prevent it: By using precise control over injection pressure and material temperature, we ensure proper flow and complete filling of the mould. Regular maintenance of moulds and runners also helps to avoid blockages that could cause short shots.
-
-
Flash
-
What it is: Flash occurs when excess plastic leaks out of the mould cavity at the parting line or ejector pin locations, forming a thin layer of material outside the desired part shape. This excess material must be trimmed off, adding time and cost to the production process.
-
How we prevent it: Flash is often the result of poorly fitted or worn moulds. Our in-house toolmaking department ensures that all moulds are manufactured to exacting tolerances. We also maintain and service the moulds regularly to prevent wear that could cause flash.
-
-
Burn Marks
-
What it is: Burn marks are dark discolourations on the surface of the part, often caused by trapped air in the mould that gets compressed and overheated, burning the plastic.
-
How we prevent it: Proper venting of the mould is essential to allow trapped air to escape. We design moulds with adequate ventilation and optimise injection speed and pressure to minimise the chance of air pockets forming.
-
-
Flow Lines
-
What it is: Flow lines are visible lines or streaks on the surface of the part, often caused by varying speeds of material flow during injection, especially when the molten plastic starts to cool before fully filling the mould.
-
How we prevent it: Flow lines are mitigated through optimal gate placement and controlling injection speed. We also use temperature-controlled moulds to ensure consistent material flow throughout the entire moulding process.
-
-
Jetting
-
What it is: Jetting occurs when the molten plastic squirts into the mould too quickly, forming a wavy pattern on the part surface. This usually happens when the material flows in a straight line rather than spreading evenly.
-
How we prevent it: By controlling the injection speed and ensuring the correct positioning of gates and runners, we prevent the plastic from jetting. Proper gate size and shape also help in distributing the material more evenly into the cavity.
-
-
Voids
-
What it is: Voids are internal air pockets within the moulded part that reduce strength and may cause the part to fail under stress.
-
How we prevent it: Maintaining consistent pressure throughout the moulding process helps to eliminate voids. We also carefully design parts to avoid thick sections where voids are more likely to form, using ribs and other design features to strengthen parts without adding bulk.
-
-
Delamination
-
What it is: Delamination is when thin layers of material peel off from the surface of the part, often due to contamination in the material or poor bonding between layers of the plastic.
-
How we prevent it: We use high-quality raw materials and carefully control the moulding conditions to prevent delamination. Regular inspection of the material for contaminants and optimising temperature and pressure also ensure proper bonding of plastic layers.
-
-
Bubbles and Blisters
-
What it is: Bubbles or blisters are caused by trapped gas or moisture within the material, leading to cosmetic flaws and potential weakness in the part.
-
How we prevent it: We use dehumidifying dryers to remove moisture from materials before moulding. Additionally, we optimise the mould design and injection speed to prevent gas from being trapped during the moulding process.
-
Key Aspects of Quality Control in Injection Moulding
-
Material Selection
The choice of plastic materials plays a significant role in the quality of injection moulded parts. At Great Central Plastics, we carefully select materials suited to the product’s requirements, whether it be strength, flexibility, or heat resistance. -
Precise Tooling
The quality of the mould directly impacts the quality of the parts produced. Our in-house toolmaking expertise allows us to create precise, durable moulds that ensure each part is formed with accuracy and repeatability. Regular maintenance of these tools is crucial to avoid defects such as flash, short shots, or sink marks. -
In-Process Monitoring
Throughout the injection moulding process, we employ real-time monitoring systems to track temperature, pressure, and other variables. This allows us to detect any irregularities and make adjustments before defects occur, ensuring that the production process remains within the desired tolerances. -
Post-Moulding Inspection
After the parts are produced, they undergo thorough inspections to ensure they meet both dimensional and aesthetic standards. Our inspection process includes visual checks, dimensional measurements, and functional testing where necessary. This final step guarantees that every product leaving our facility is of the highest quality.
The Role of ISO 9001:2015 in Quality Assurance
As an ISO 9001:2015 certified company, Great Central Plastics follows a stringent quality management system that is internationally recognised. This certification demonstrates our commitment to maintaining high standards and continually improving our processes. It ensures that every part we produce meets customer specifications and complies with industry regulations.
Benefits of Quality Control for Your Business
By implementing rigorous quality control in injection moulding, we help businesses avoid costly production errors and delays. Consistent quality also enhances brand reputation, particularly in sectors where safety and performance are paramount. Whether you need high-volume production or small bespoke orders, our commitment to quality ensures reliable results every time.
At Great Central Plastics, we don't just manufacture injection moulded parts—we partner with our customers to deliver solutions that meet their exact needs. Our robust quality control measures, backed by ISO 9001:2015 certification, guarantee the exceptional standards you expect from a leading injection moulding company.
Ready to see the difference quality makes? Contact us today to discuss your project requirements and learn how our expertise can help bring your vision to life.
For more information on The Importance of Quality Control in Injection Moulding talk to Great Central Plastics Ltd