
Sign In
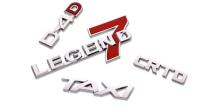
Transforming Your Injection Mouldings with Chrome Plating: A Comprehensive Overview
As a manufacturer in the automotive industry, we know just how important it is to produce high-quality injection mouldings. After all, they are critical components for many automotive parts. Over the years, we have found that one of the best ways to enhance the appearance and durability of these mouldings is to use chrome plating. In this article, we will provide a comprehensive overview of how chrome plating can transform your injection mouldings.
Introduction to Injection Moulding and Chrome Plating
Before we dive into the benefits of chrome plating for injection mouldings, let's first understand what injection moulding and chrome plating is. Injection moulding is a manufacturing process that involves melting plastic pellets and injecting the molten material into a mould. The material then cools and solidifies to form the desired shape. On the other hand, chrome plating is a process of electroplating a thin layer of chromium onto a metal or plastic surface to enhance its appearance and durability.
Benefits of Chrome Plating for Injection Mouldings
Chrome plating offers several benefits for injection mouldings. Firstly, it enhances the appearance of the mouldings by giving them a shiny, metallic finish. This is particularly useful for automotive parts such as grilles, mirrors, door handles, and badges where appearance is a critical factor. Secondly, chrome plating improves the durability of the mouldings by making them resistant to corrosion, wear, and scratches. This is especially important for automotive parts that are exposed to harsh weather conditions and road debris.
Applications of Injection Moulding and Chrome Plating in the Automotive Industry
The automotive industry is one of the biggest users of injection mouldings and chrome plating. Injection mouldings are used in a wide range of automotive parts, including interior and exterior trims, lighting components, and engine parts. Chrome plating is also used extensively in the automotive industry to enhance the appearance and durability of these parts.
One example of chrome plating in the automotive industry is the use of chrome-plated grilles or exterior badging. These parts are a common feature in many cars and are often the first thing that people notice. Chrome plating gives these parts a shiny, reflective finish that enhances the overall appearance of the car. Additionally, the chrome plating protects the parts from corrosion and wear, ensuring that they last for many years.
Chrome Plating Process: Step-by-Step Overview
The chrome plating process involves several steps. Firstly, the surface of the injection moulding is cleaned and prepared to remove any dirt, oil, or other contaminants. Next, the moulding is coated with a layer of nickel, which serves as a base layer for the chrome plating. The nickel layer is then electroplated with a thin layer of chromium, which gives the moulding its shiny, metallic finish.
After the chrome plating is complete, the moulding is rinsed and dried to remove any excess chemicals. The chrome plating process is a complex and highly technical process that requires specialised equipment and expertise.
Factors to Consider when Choosing Injection Moulding and Chrome Plating Materials
When choosing materials for injection moulding and chrome plating, there are several factors to consider. Firstly, the material must be suitable for the application and meet the required performance specifications. Secondly, the material must be compatible with the chrome plating process and not react with the chemicals used in the process. Finally, the cost of the material must also be taken into account, as this can have a significant impact on the overall cost of production. Our specialist team will be able to help guide you on which polymer to choose for your injection moulded parts.
Quality Control in Injection Moulding and Chrome Plating
Quality control is a critical aspect of injection moulding and chrome plating. Manufacturers must ensure that their products meet the required performance and appearance standards. This involves testing the products at various stages of production to ensure that they meet the required specifications.
In injection moulding, quality control involves monitoring the moulding process to ensure that the parts are produced to the correct dimensions and have the required mechanical properties. In chrome plating, quality control involves testing the thickness and adhesion of the chrome layer to ensure that it meets the required standards.
Future of Injection Moulding and Chrome Plating in the Automotive Industry
As the automotive industry continues to evolve, we can expect to see more innovative applications of injection moulding and chrome plating. With the right materials and quality control measures, we as a manufacturer can produce high-quality injection mouldings that meet the demands of the automotive industry. Please get in touch to discuss your project requirements.
For more information on Transforming Your Injection Mouldings with Chrome Plating: A Comprehensive Overview talk to Great Central Plastics Ltd
Enquire Now
List your company on FindTheNeedle.