
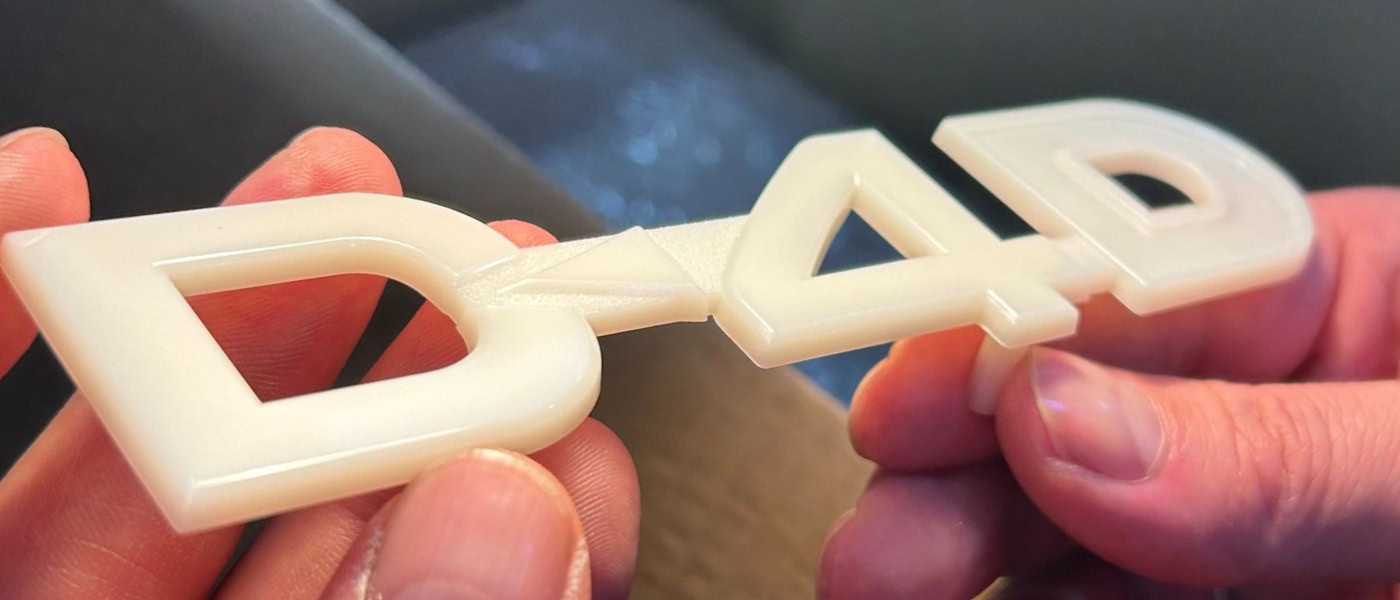
In the automotive industry, the manufacturing method used for producing badges is a critical factor that impacts quality, durability, and cost-efficiency. Among various manufacturing techniques, injection moulding has become the preferred choice for automotive badges due to its numerous advantages. While other methods like die-casting, stamping, or 3D printing exist, injection moulding stands out for its ability to consistently deliver high-quality badges at scale. At Great Central Plastics, we specialise in injection moulding, offering decades of experience to automotive manufacturers across the UK.
Why Injection Moulding?
Injection moulding is the go-to method for automotive badge production because it excels in several key areas: precision, durability, and cost-effectiveness. It has become the standard in the industry, not because other methods don't work, but because injection moulding offers unmatched efficiency and results, particularly for high-volume manufacturing. Below, we explore why this method is so effective and how it compares to alternatives.
Precision and Consistency
One of the standout advantages of injection moulding is its precision. This technique involves injecting molten plastic into a mould cavity, which solidifies into the desired shape. The result is an automotive badge with highly accurate dimensions and consistent quality across every unit. This is especially important for badges that must fit perfectly onto vehicles and maintain a uniform appearance. Compared to alternatives like stamping or die-casting, injection moulding offers superior consistency, especially for complex designs. At Great Central Plastics, our advanced machinery and in-house toolmaking capabilities ensure that each badge meets the exacting standards of the automotive industry.
Durability and Longevity
Automotive badges must endure various environmental challenges, including temperature extremes, UV exposure, and contact with chemicals. Injection moulding allows us to use high-performance polymers that are specifically engineered to withstand these conditions. In contrast, other methods like die-casting may produce parts that are more prone to corrosion or wear over time. Whether you need traditional plastics or innovative bio-based materials, injection moulding provides the durability needed to ensure that your badges remain in excellent condition throughout the life of the vehicle. This long-term reliability makes injection moulding the preferred choice for manufacturers who want their products to last.
Cost-Effective Production
For manufacturers, controlling costs while maintaining quality is essential. Injection moulding offers an efficient and economical production process, especially for large-scale orders. With short cycle times and the ability to produce large quantities in a single run, injection moulding minimises production costs per unit. Compared to methods like 3D printing, which is often used for prototyping but can be time-consuming and expensive for mass production, injection moulding shines as the most cost-effective option for large-scale badge production. At Great Central Plastics, our fully automated facilities allow us to produce badges around the clock, ensuring that we meet your production needs while keeping costs down.
Customisation and Finishes
Injection moulding isn’t just about mass production; it also offers significant opportunities for customisation. From chrome plating and spray painting to resin decals and coloured inserts, injection moulding allows for a variety of finishes that cater to your brand’s aesthetic requirements. This level of customisation is difficult to achieve with other manufacturing methods, which often involve additional steps or processes to achieve similar results. At Great Central Plastics, our expertise in custom finishes ensures that your automotive badges are not only functional but also visually striking.
Alternatives to Injection Moulding
While injection moulding is the preferred method, it's important to acknowledge the alternatives and where they might be appropriate:
-
Die-Casting: Often used for metal badges, die-casting involves forcing molten metal into a mould. While it produces strong and durable products, it's typically more expensive and less suitable for complex plastic designs.
-
Stamping: This method is common for simpler, flat metal badges. However, it lacks the versatility and detail achievable with injection moulding and often requires additional processes to add colour or texture.
-
3D Printing: Ideal for prototypes or small production runs, 3D printing offers high levels of customisation. However, it is much slower and less cost-effective for mass production compared to injection moulding.
These alternatives have their places, but for large-scale production of durable and detailed badges, injection moulding remains unmatched.
Sustainable Manufacturing
As the automotive industry increasingly embraces sustainability, injection moulding offers notable environmental benefits. At Great Central Plastics, we prioritise eco-friendly practices, using recycled and plant-based materials where possible. Our sustainable approach reduces waste and energy consumption, which is crucial in today’s automotive industry. Compared to traditional manufacturing methods, injection moulding’s efficiency and ability to incorporate sustainable materials make it a greener choice for badge production.
Partner with Experts in Automotive Badges
Choosing the right partner for your automotive badge production is just as critical as selecting the manufacturing method. At Great Central Plastics, our decades of experience in injection moulding, combined with our commitment to sustainability and innovation, make us the ideal choice for manufacturers seeking high-quality badge solutions. We have worked with leading automotive brands across the UK and beyond, delivering badges that meet and exceed industry standards.
Conclusion
Injection moulding is the preferred method for producing automotive badges due to its precision, durability, and cost-effectiveness. While other manufacturing methods have their uses, injection moulding stands out for its ability to deliver consistent, high-quality products at scale. At Great Central Plastics, we are committed to providing top-tier injection-moulded automotive badges that meet your brand’s unique needs. Contact us today to find out how we can support your next automotive badge project.
For more information on Why Injection Moulding is the Preferred Method for Automotive Badges talk to Great Central Plastics Ltd