
What is sheet metal fabrication?
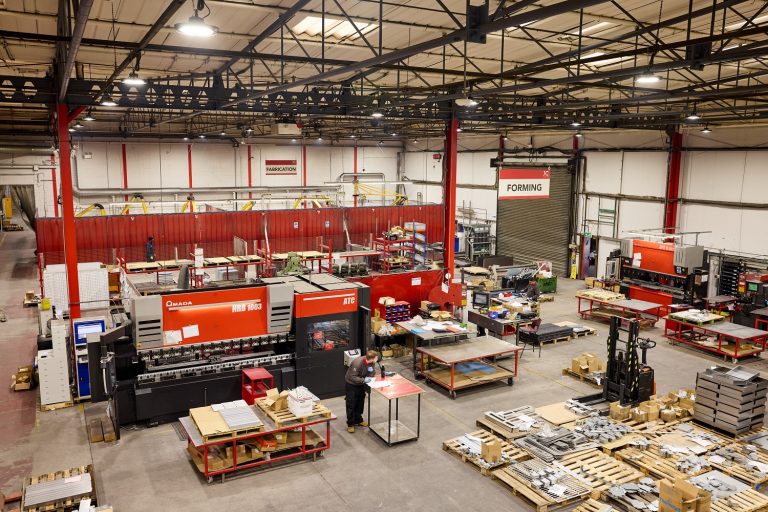
What is sheet metal fabrication?
Sheet metal fabrication is the process of converting flat sheets of metal, such as steel, aluminium, or copper, into three-dimensional components or structures. This process involves a combination of cutting, bending, forming, welding, finishing and assembly techniques to create a vast array of products across industries. From automotive components to electronic enclosures, the applications of sheet metal fabrication are virtually limitless.
What is the sheet metal fabrication process?
The sheet metal fabrication process typically involves the following key steps:
- Design and Planning
The initial phase in sheet metal fabrication involves transforming a concept into a tangible product design drawing. This stage is critical for ensuring the final product meets the desired specifications. CAD software is employed to create detailed 2D and 3D models, allowing for thorough visualisation and analysis of the design.
Careful consideration is given to factors such as material selection, dimensions, tolerances, and manufacturing costs to optimise the fabrication process. Moreover, design for manufacturability (DFM) principles are applied to identify potential challenges and make necessary adjustments for efficient production.
- Material Selection
Selecting the appropriate metal for a sheet metal fabrication project is paramount to achieving the desired properties and performance. A wide range of metals, including steel, aluminium, stainless steel, and galvanised, offer distinct characteristics such as strength, weight, corrosion resistance, and conductivity.
Factors like the intended use of the product, environmental conditions, and budgetary constraints influence the material choice. Additionally, the availability and cost of different metals play a role in the decision-making process.
Choosing the right metal for the application is crucial. Common sheet metal materials include:
- Steel: Known for its strength and durability, steel is widely used in construction, automotive, and appliance industries.
- Aluminium: Lightweight and corrosion-resistant, aluminium is preferred for aerospace, automotive, and marine applications.
- Stainless Steel: Offers excellent corrosion resistance and durability, making it suitable for food processing, medical equipment, and architectural applications.
- Galvanised and Zinctec: Possessing high thermal and electrical conductivity, is used in electronics, HVAC systems, and enclosures.
- Cutting
This process involves cutting or punching the sheet metal into the required shapes and sizes. Various techniques are employed based on the desired precision, material thickness, and complexity of the design. Punching and fibre laser cutting are commonly used methods. While punching creates precise holes or shapes. Laser cutting offers exceptional accuracy and versatility, allowing for intricate designs.
- Bending
Bending is a crucial step in shaping sheet metal into desired angles or curves. This process involves applying pressure to the metal to create the desired form. Press brake bending is a widely used method that employs a press and a brake to bend the metal to specific angles.
Brake forming offers greater flexibility for complex shapes, while roll forming is suitable for producing long lengths of consistently shaped profiles. The bending process requires careful consideration of material properties, bend radius, and tooling to achieve the desired results.
The metal is formed into desired angles or curves using bending processes:
- Press Brake Bending: A machine that bends metal sheets using a press and a brake.
- Automatic panel Benders
- Roll Forming: Creates continuous lengths of formed metal profiles.
- Welding
Welding is the process of joining metal components together to create a strong and durable bond. Various welding techniques are available, each with its own advantages and applications. MIG welding and TIG welding are common methods that involve melting the base metal and filler material to create a fusion zone.
Spot welding is suitable for joining thin metal sheets at specific points. The choice of welding process depends on factors such as material type, thickness, joint design, and desired strength.
- Finishing
The final stage of sheet metal fabrication involves finishing processes to enhance the product’s appearance, functionality, and durability. Deburring removes sharp edges and burrs to prevent injuries and improve product safety. Grinding smoothens surfaces and removes imperfections, while polishing creates a desired finish, ranging from matte to mirror-like.
Powder Coating is applied to protect the metal from corrosion, wear, and environmental factors, as well as to enhance aesthetics. The choice of finishing processes depends on the product’s intended use and customer requirements.
- Assembly
The assembly process involves joining fabricated components into the final product. This may include bolting, riveting, or using other fastening methods. For complex assemblies, jigs and fixtures are often used to ensure accuracy and consistency. Careful attention is paid to component alignment and fit to achieve the desired product functionality.
- Packaging
Proper packaging is essential to protect the finished product during transportation and storage. Packaging materials are selected based on product size, weight, and fragility. Protective packaging elements such as cushioning, bracing, and sealing are used to prevent damage. Clear labelling with product information and handling instructions is crucial for efficient logistics.
- Storage and Dispatch
Effective storage ensures product integrity until shipment. Storage conditions should be controlled to prevent damage from factors such as humidity, temperature fluctuations, and physical impact. Inventory management systems are used to track product location and availability.
Dispatch involves coordinating transportation and delivery to customers. Shipping methods are chosen based on product characteristics, delivery timelines, and cost considerations.
What are the advantages of assembly in sheet metal fabrication?
Assembly is a crucial stage in transforming individual sheet metal components into a complete product. This process offers several advantages:
- Product Functionality: By combining different components, assembly creates products with specific functions and purposes.
- Enhanced Structural Integrity: Assembling components reinforces the overall structure, improving its strength and durability.
- Customisation: Assembly allows for customisation by combining various components in different configurations.
- Value Addition: Converting raw materials into a finished product increases its value significantly.
- Efficiency: Streamlined assembly processes improve production efficiency and reduce lead times.
- Quality Control: Assembly provides an opportunity to inspect components for defects and ensure the final product meets quality standards.
- Cost-Effectiveness: Efficient assembly can optimise material usage and reduce overall production costs.
- Versatility: Assembly techniques can be adapted to various product designs and complexities.
By effectively managing the assembly process, sheet metal fabricators can maximise the potential of their products and achieve desired outcomes.
What are the advantages of sheet metal fabrication?
- Versatility: Sheet metal can be formed into a wide range of shapes and sizes.
- Cost-Effective: Often more economical than other manufacturing methods.
- Lightweight: Many metals used in sheet metal fabrication offer excellent weight-to-strength ratios.
- Durability: Sheet metal products are known for their strength and longevity.
- Precision: Modern fabrication techniques allow for high levels of accuracy and consistency.
Where can sheet metal fabrication be applied?
The applications of sheet metal fabrication are vast and diverse:
- Automotive Industry: Car bodies, chassis components, exhaust systems, and other parts.
- Electronics Industry: Enclosures, brackets, heat sinks, and chassis.
- Construction Industry: Ductwork, roofing, cladding, and structural components.
- Appliance Industry: Kitchen appliances, HVAC systems, and refrigeration units.
- Medical Industry: Surgical instruments, hospital equipment, and medical devices.
- Aerospace Industry: Aircraft components, satellite parts, and rocket components.
- Agriculture Industry: Farm equipment, storage tanks, and silos.
What are the challenges in sheet metal fabrication?
While sheet metal fabrication offers numerous advantages, it also presents some challenges:
- Material Limitations: The choice of metal can affect the formability and strength of the product.
- Tooling Costs: Developing custom tooling for complex shapes can be expensive.
- Labor Intensive: Some fabrication processes require skilled labour.
- Environmental Impact: Manufacturing processes can generate waste and emissions.
To address these challenges, manufacturers are increasingly adopting advanced technologies such as computer-aided manufacturing (CAM), robotics, and automation.
Hear from our experts
Let’s hear from Vijay Lakhnsi, Technical Support in the Fabrication Department.
I’ve been with JC Metalworks since 2004 and have witnessed firsthand the advancements in sheet metal fabrication.
By investing in state-of-the-art technology and embracing digitalisation, JC Metalworks has streamlined its processes and consistently delivered exceptional sheet metal projects. It’s an honour to be part of a company that continues to set the industry standard for quality, innovation, and customer satisfaction.
In conclusion, sheet metal fabrication is a dynamic and essential process that plays a vital role in modern manufacturing. By understanding the various techniques and applications, businesses can leverage the benefits of sheet metal to create innovative and high-quality products.
Sheet metal fabrication is a multifaceted process that involves a seamless integration of design, engineering, and manufacturing expertise. From the initial concept to the final product, each stage is critical in delivering high-quality and functional solutions.
JC Metalworks excels in this domain by embodying the principles outlined in this blog. With a deep understanding of sheet metal properties, cutting-edge technology, and a skilled workforce, we deliver exceptional sheet metal fabrication services. Our commitment to precision, efficiency, and customer satisfaction sets us apart as a leading provider in the industry.
Whether you require intricate components or large-scale assemblies, JC Metalworks offers comprehensive solutions tailored to your specific needs. Contact us today to discuss your project and experience the difference our expertise can make.
For more information on What is sheet metal fabrication? talk to JC Metalworks