
What Are CPFG Panels? A Comprehensive Guide to Their Purpose and Evolution in Offshore Safety
05-12-2024
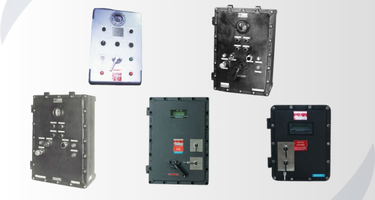
JCE has been a leader in hazardous area safety systems since the development of its Combined Pressurization Fire and Gas (CPFG) control panel in 1982. JCE was the original developer of this critical technology, providing robust protection for offshore oil and gas installations.
At the time, significant discussions with JCE, Lloyds and DNV raised concerns about the lack of adequate safety measures in hazardous environments. JCE responded by creating the CPFG panel, which introduced a groundbreaking safety solution, transforming industry standards. Early adopters, including Vertec, Labtech, Consafe, Coruweld, and many other service companies quickly recognised the system's importance and its potential to make offshore environments significantly safer.
The Evolution of CPFG Panels
Over the years, JCE has continuously advanced its CPFG panel technology, with each generation improving upon its predecessor. The CPFG panel integrates three core safety functions—pressurisation control, fire detection, and gas detection—into a single system, offering a comprehensive safety solution for offshore installations.
JCE is now on the cusp of launching the 5th Generation of CPFG panels, marking another significant leap in offshore safety technology.
Here's the evolution:
- 1st Generation – Relays/Contactors/Timers: The first version utilised basic relays, contactors, and timers to manage pressurisation, fire, and gas detection, laying the foundation for future advancements.
- 2nd Generation – Gas Monitor/Gas Master: This version introduced enhanced gas detection accuracy and a simplified LED indication display behind a window interface for more efficient monitoring and detailed information.
- 3rd Generation – PLB/ADIB CPFG2000: The CPFG-2000 featured a modern interface and improved monitoring and control capabilities. JCE developed a custom PLB & ADIB printed circuit control boards complete with a VFD display allowing for even more information to be displayed to the operator, making safety management more efficient in larger installations.
- 4th Generation – CPFG-3000 & CPFG-4000: The CPFG-3000 & CPFG-4000 introduced Programmable Logic Controllers (PLCs), significantly improving system automation and monitoring. It included a backlit HMI display for easier configuration, Galvanic Isolation for intrinsic safety, and the ability to monitor up to three gas channels (channel 3 customisable to H2S) and one fire channel simultaneously. The HMI featured a fully graphical 3 inch display as allowing the operator to adjust settings within the HMI itself. The system was compatible with both pellistor and infrared gas detectors and offered comprehensive fire detection capabilities. The CPFG-3000 featured a 63 Amp main contactor where the CPFG-4000 features a 40 Amp contactor allowing the use of a smaller enclosure where space restraints may apply.
- 5th Generation – Coming Soon: The latest generation will feature cutting-edge software and state-of-the-art technology, offering improved safety, reliability, and operational efficiency all combined with a customisable 4 inch touchscreen HMI. While details remain confidential, the new system promises advanced diagnostics and remote capabilities to meet the evolving needs of offshore environments.
What Are CPFG Panels?
A CPFG panel is a critical safety system designed to integrate pressurisation control, fire detection, and gas detection into one unit, specifically tailored for hazardous environments like offshore oil and gas installations. Its primary role is to continuously monitor these safety parameters, providing early warnings or automatic responses to potential hazards to allow the user to create a safe area within a hazardous environment to operate standard equipment.
Application of CPFG Panels
JCE’s CPFG panels are critical for ensuring safety in environments where flammable gases, vapours, or liquids are present. They are especially valuable in:
- Offshore Installations: Deployed in zoned cabins, ROV control vans, driller control cabins, accommodation modules and MWD (Measurement While Drilling) modules.
- Hazardous Areas: Designed for hazardous areas classified as Zone 1 or Division 1, ensuring safety in environments prone to explosive gases and vapours.
- Control Rooms and Workshops: Used to maintain positive pressure in control rooms and other confined areas like workshops or office modules, preventing the ingress of hazardous gases.
- Remote Monitoring: These panels enable remote monitoring of offshore installations, ensuring safety in unmanned or minimally staffed locations.
By combining these safety functions into a single system, JCE’s CPFG panels enhance both safety and operational efficiency in hazardous environments.
Manufacturing Process of JCE CPFG Panels
The manufacturing process of JCE’s CPFG panels involves several crucial steps to ensure system quality, reliability, and compliance with international safety standards:
- Design and Engineering: Each panel is designed to meet specific project requirements and safety standards. Components such as gas detectors, smoke detectors, pressure switches and fire alarms are carefully selected during this phase.
- Component Integration: Selected components are integrated into a unified system housed in Ex d flameproof enclosures, ensuring compliance with ATEX and IECEx certifications.
- Assembly: The panels are assembled using PLC-based controllers (as seen in the CPFG-3000 and upcoming CPFG-5000), with additional integration of pressure sensors, fire suppression controls, and gas detectors.
- Software Programming: The system's software is programmed to monitor and control pressurisation, fire detection, and gas safety parameters, allowing for customisation based on specific installation needs. Individual gas levels, purge times, shutdown times, flow rates etc can be set by the user via the HMI.
- Rigorous Testing: Each panel undergoes extensive functional testing under simulated conditions, including fire and gas detections, ensuring operational effectiveness. Certification testing guarantees adherence to safety standards.
- Quality Control: Strict quality control measures are followed throughout the production process, ensuring optimal performance of every component and subsystem.
- Certification and Compliance: The final step involves certification to international safety standards, ensuring the CPFG panel is fully compliant with ATEX and IECEx regulations. Every CPFG is supplied with a certification pack & operation manual.
How CPFG Panels Work
A CPFG panel integrates pressurisation, fire detection, and gas detection within offshore installations. Its core functions include:
1. Pressurisation Control: Maintains positive pressure via a pressurisation fan after a purge cycle, in enclosures like control rooms, preventing hazardous gases from entering. Pressure sensors continuously monitor conditions.
- Fire Detection: Uses smoke, heat, MAC and flame detectors to monitor for fire risks. The system activates alarms and may trigger fire suppression systems, such as sprinklers or CO₂ flooding.
- Gas Detection: Monitors for the presence of hazardous gases, like hydrocarbons. The system triggers alarms at customisable setpoints and initiates shutdown procedures if dangerous levels are detected. Facility for individual or voting can also set on the HMI.
- Integrated Operation: All functions are controlled through a single interface, allowing operators to manage safety parameters in real-time. Automated emergency shutdowns are activated if critical conditions are met.
- Maintenance and Diagnostics: CPFG systems include self-testing features, event logging, and detector fault monitoring to ensure continued reliability. Diagnostics help pre-empt issues before they escalate. A maintenance mode is available.
Benefits of JCE CPFG Panels
JCE’s CPFG panels provide several important benefits:
- Enhanced Safety: By integrating multiple safety functions, CPFG panels offer real-time protection and automated responses to hazards, ensuring swift resolution of dangerous situations.
- Cost Efficiency: Combining three safety functions into one system reduces installation and maintenance costs, providing long-term savings.
- Reliability: Built to withstand harsh offshore conditions, CPFG panels feature HMI displays with user feedback for simple set up and monitoring. Our CPFG Enclosures have proven over the many generations to be a robust, reliable & easy to use system.
- Regulatory Compliance: All JCE CPFG panels meet stringent global safety standards, including ATEX and IECEx certifications.
- Minimised Downtime: Real-time monitoring and remote diagnostics enable faster issue detection, reducing downtime. Automatic shutdowns ensure personnel and equipment safety during hazards.
- Customisability: The CPFG3000 and CPFG4000 offer configurable gas channels, fire detection zones, and system bypass options, making them adaptable to unique installation requirements.
- Environmental Protection: Early gas detection and fire prevention reduce the risk of catastrophic incidents, protecting the surrounding environment.
Conclusion
Since 1982, JCE’s CPFG panels have played a crucial role in improving offshore safety. From the first-generation systems to the forthcoming CPFG-5000, JCE has continuously led innovation in hazardous area safety. By integrating pressurisation control, fire detection, and gas monitoring into a single, efficient system, JCE’s CPFG panels offer unmatched protection and operational efficiency. With a commitment to innovation and safety, JCE remains the trusted choice for safeguarding personnel, assets, and the environment in the most hazardous environments.
For more information on What Are CPFG Panels? A Comprehensive Guide to Their Purpose and Evolution in Offshore Safety talk to JCE Group (UK) Ltd