
Sign In
Gravity Infeed & Outfeed System
19-11-2019
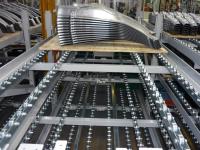
Case Study
Futaba (Car Component Manufacturer), Burnley
Futaba Manufacturing UK Ltd (Burnley), who produce steel components for one of the world’s largest car producers, had their facility full of fork trucks and steel stillages. There were 2 distinct areas which needed to be looked at. Firstly, the health and safety implication of the sheer amount of fork trucks travelling around the facility, and secondly, their need to organise and increase productivity.
After initial trials, using simple gravity tracking (rollers), it was obvious that a more bespoke system was required, given that we needed to utilise 2 and 3 tiered conveying, coupled with trying to achieve a more cost effective result.
As the tote bins (weighing around 20Kgs) and wooden slave boards (weighing around 200Kgs) were flat bottomed, the first 2 cells were installed using a mixture of steel and plastic skatewheels, which worked incredibly well.
The rest, as they say, is history. In total, Futaba’s capital outlay for both phases of the system was in excess of £600,000, with increases in efficiency and organisation/planning, together with a much safer and aesthetically pleasing materials handling solution.
For more information on Gravity Infeed & Outfeed System talk to Mobility Engineering
Enquire Now
List your company on FindTheNeedle.