
Sign In
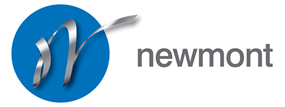
Senior Inspector / Team Leader
Job Holder: Senior Inspector / Team LeaderReports to: Acting Quality Manager / Managing Director
Job Purpose:
The job holder is responsible for upholding and setting quality standards in line with customer standards and practices in all aspects of the companies work and to ensure a timely dispatch of products through efficient delegation and prioritisation of work and tasks.
Main Responsibilities: (Refer Appendix A for details)
- Inspection of precision parts using conventional measurement equipment and CMMs to ensure accuracy of dimensions and tolerances stated upon drawings and routings.
- Checking accuracy of all documentation relating to products and these could include but not limited to: Works Orders(routings), CMM/GMM reports, Supplier Documentation, Certificate of Conformities (CofC’s), First Article’s (FAIR’s), Control Plans, Drawings, Standards, Procedures, Rejections and Customer Complaints etc.
- Programme, manage and use the CMM and other equipment to ensure that products conform to requirements.
- Research and implement improved inspection practices that drive an improvement to quality internally such as failure rates at 1st offs and Final inspections. Look at how we can adopt the use of sampling techniques to minimize the time in inspection and push inspection back to the operators.
- Compile FAIR’s in line with AS9102.
- Maintain calibration system ensuring that it’s up to date at all times.
- Be involved in all supplier and customer returns making sure that all are entered onto javelin and the relevant paperwork is raised.
- Maintain an effective gate system whereby no defects are sent to the customer.
- Adherence to Company’s Quality Management System and exception reporting procedures at all times.
- Communicate with customers and suppliers as and when needed in supporting with quality issues.
- Participation in regular audits to maintain standards and preserve ISO:9001 certification.
- Adherence to Company Health and Safety requirements and follows Company rules and acceptable codes of conduct.
- Man management of department ensuring utilization of staff and booking times are maintained to standard.
Required Knowledge, Skills and Abilities:
- Proficient in the use of hand measurement tools.
- Experience of using a Co-ordinate Measuring Machine (CMM/GMM).
- Ability to read engineering drawings and have knowledge of GD&T.
- Knowledge and experience in compiling inspection reports.
- Quality control with ISO9001/AS9100
- Familiarity with Auditing processes and procedures.
- Proficiency in Computer Programming (CMM) and IT systems.
- Meticulous attention to detail
- Excellent Communication skills
- Methodical & Process driven
- Excellent time management
- Experience in calibration
Educational Requirements/Experience:
- Higher Education Qualification in Engineering and experience/knowledge of precision engineering.
- Thorough understanding of geometric dimensioning, working to very fine tolerances and reading detailed specifications.
- Experience as a Quality Inspector / Quality Engineer in CNC machining and precision manufacturing environment.
- Machine shop or Tool room experience with thorough knowledge of practices, engineering principles and operations.
- Experience working with high grade metallic materials.
- Knowledge of a range of CNC processes including turning, milling, grinding. Spline & gear production
- Able to present themselves detailed reports to customers and suppliers.
Appendix A
Principle Duties and Responsibilities
Core Activities
Inspection
- To prioritise work through the department to ensure all work is completed in an efficient order, to return First Offs to the workshop promptly, and that all production and delivery deadlines are met.
- Delegate work to colleagues in order to satisfy the above point and in line with their skill set / abilities.
- Work with production staff to resolve issues with Non-Conforming parts.
- To follow inspection functions in accordance with the documented procedures.
- To return products promptly to manufacturing, after inspection, for the next operation with the appropriate controlling documentation.
- To programme and operate CMM machines.
Quality Control
- To assist the line manager in controlling non-conforming material and to take appropriate corrective action.
- To identify all non-conforming material after inspection and segregate from conforming material.
- To inspect products according to the current issue product documentation ensuring that quality standards are achieved.
- To inform the line manager of any defects and recommend corrective actions and follow through to minimize lost production time.
- To check when using equipment that it is within calibration and, if not, make arrangements tore-calibrate the equipment.
- To maintain the controls upon non-conforming material to ensure, in liaison with the line manager, that prompt and effective corrective actions are performed.
- To prepare FAIRs or ISIRs and provide First Off Inspection reports.
Documentation
- To ensure that the records and reports of all failures are identified and approved for customer returns, supplier returns and “In-House” rejects.
- To manage and control the product documentation within the inspection department.
- To log customer returns for investigation purposes.
- To follow and record all inspection functions in accordance with company “Inspection Procedures”.
- To record all inspection activities including rejections and repair actions upon Routing Sheet Inspection Records.
- Complete relevant forms / reports relating to Non-Conforming products, i.e Reject reports, NCR’s Corrective action plans etc.
- To prepare First Article Inspection Reports(FAIR) according to customer specifications/requirements.
IT Skills
- Be able to use the production control system to retrieve information relevant to the inspection department, i.e delivery dates, delivery history, part issue changes, customer & supplier returns.
- Be able to use Outlook to communicate with customers & suppliers
- Be able to retrieve information located on the IT Network, i.e. drawings, old inspection records etc.
- Be competent in the use of Word and Excel to produce reports to customers’ requirements.
Support Activities
Training
- To train and assist staff in the operation of all inspection equipment.
List your company on FindTheNeedle.