
What is Vacuum Forming? A Complete Guide
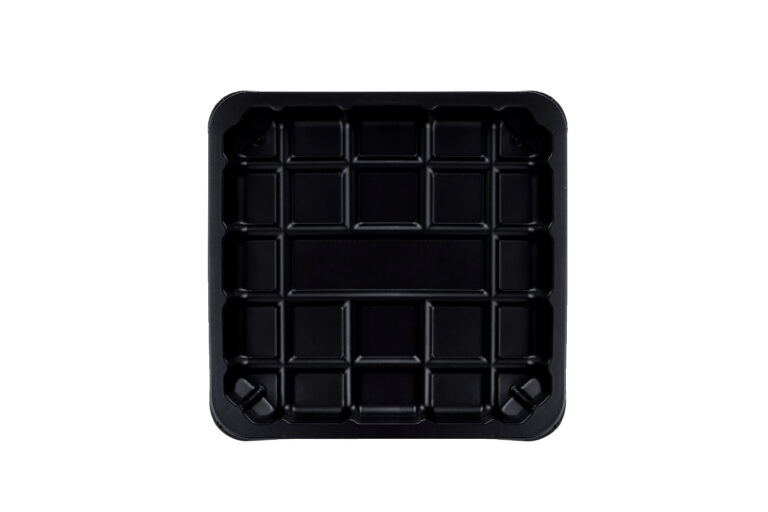
Overview
Vacuum forming is a versatile manufacturing process used to shape plastic sheets into a range of products, from packaging to automotive components. It involves heating a plastic sheet, forming it over a mould, and using vacuum pressure to create the desired shape. In this guide, we’ll explore the materials, types of moulds, applications, and the advantages and limitations of vacuum forming.
If you’re planning a vacuum forming project and want to find the best suppliers in the UK and Ireland, PlastikCity can help you easily compare quotes from vetted suppliers. Request a quote for your upcoming project and ensure you’re working with the right partner.
The Vacuum Forming Process Explained
The vacuum forming process involves multiple steps to ensure the plastic is shaped accurately and with the required detail. Here’s an in-depth look at each stage:
Clamping: To start, a plastic sheet is clamped securely in place within the machine. The clamps must be strong enough to hold the sheet steady during heating and forming. Vacuum forming can accommodate sheets of various thicknesses, typically up to 6mm with a single heater or up to 10mm with twin heaters. Ensuring the plastic is firmly clamped helps maintain precision in the final shape.
Heating: Once clamped, the plastic sheet is heated to its forming temperature. Infrared or quartz heaters are commonly used for this stage, allowing for even heating across the sheet’s surface. Consistent heating is essential for achieving the best results, as uneven heating can lead to weak spots or distortions. Higher-end machines may have zoned heating controls to allow for precise adjustments, ensuring each area of the sheet receives the correct amount of heat.
Pre-stretching (Optional): On some machines, pre-stretching (also known as “bubbling”) is used to help control the material’s thickness. This involves slightly inflating the heated plastic sheet, creating a bubble shape before it meets the mould. Pre-stretching ensures even wall thickness, which is particularly useful when the final part requires consistent strength throughout.
Vacuum Application: With the plastic now at the optimal forming temperature, the sheet is positioned over the mould, and a vacuum is applied. The vacuum pump removes the air between the sheet and the mould, creating a strong suction that pulls the plastic tightly against the mould surface. For larger parts, or where rapid forming is needed, a vacuum reservoir may be used to ensure a powerful, consistent vacuum that maintains the shape as the plastic cools.
Cooling and Release: After forming, the plastic must cool and solidify before it can be safely removed from the mould. If the part is released too early, it may deform or lose detail, so cooling is critical. Some machines use high-speed fans or a misting system to accelerate the cooling process, particularly when working with thicker or crystalline plastics that take longer to cool.
Trimming and Finishing: Once fully cooled, the formed plastic is removed from the mould, but it may have excess material around the edges. This trimming stage removes unnecessary plastic, leaving a clean, finished product. Trimming can be done using different methods, including CNC cutting, guillotining, or press cutting, depending on the shape, material, and level of detail required. Additional finishing steps, such as drilling or printing, may also be applied if the product needs holes, slots, or decorative elements.
The vacuum forming process is highly adaptable, making it ideal for both short and long production runs. It allows for quick adjustments to design, meaning that complex shapes can be achieved relatively easily with the right equipment.
Materials Used in Vacuum Forming
In vacuum forming, a range of thermoplastics can be used depending on the desired properties of the final product. Here are some of the most common materials:
ABS (Acrylonitrile Butadiene Styrene): Known for its durability and impact resistance, ABS is ideal for products like shower trays and vehicle interior parts that need to withstand regular use and potential impact.
PETG (Polyester Copolymer): This material is popular in medical and food packaging as it can be easily sanitised, making it safe for contact with food and medical items.
Polystyrene (PS): Widely used for disposable items like yoghurt pots and packaging, polystyrene offers a balance of affordability and rigidity, suitable for single-use products.
HDPE (High-Density Polyethylene): HDPE is durable and weather-resistant, often chosen for outdoor products and containers. Its strength and chemical resistance make it a great option for industrial components as well.
PVC (Polyvinyl Chloride): A versatile plastic that can be used for a variety of applications, PVC works well for industrial parts and is resistant to impact and chemical wear, adding longevity to products that need a tougher plastic.
PMMA (Acrylic): Acrylic is popular for its clarity and aesthetic appeal, commonly used in signage, displays, and protective barriers. It offers good resistance to weathering and UV exposure, making it a go-to for outdoor applications.
Each material brings unique benefits to the vacuum forming process, and selecting the right one depends on the application’s durability, safety, and appearance requirements.
Types of Moulds for Vacuum Forming
Male vs. Female Moulds
Male Moulds: These convex moulds shape the inner surface of the plastic part.
Female Moulds: These concave moulds form the outer dimensions of the plastic, providing more detail for parts that need precise external shapes.
3D Printed Moulds for Rapid Prototyping
3D printed moulds are a fast, affordable option for short runs or prototypes. They provide flexibility to test and modify designs without heavy costs, making them a good choice for designers exploring new concepts.
Traditional Mould Types
Modelling Clay Moulds
Clay is ideal for quick prototypes but isn’t durable enough for repeated use, as it can crack or wear under heat.
Wooden Moulds
Wood moulds are durable, affordable, and easy to shape, making them suitable for longer runs of simple designs. They may warp with extensive use, but using strong woods can help increase their lifespan.
Cast Aluminium Moulds
Aluminium moulds are durable and precise, making them perfect for high-volume runs. However, they take longer to produce and are more costly, making them best suited for industrial applications.
Structural Foam Moulds
Structural foam is a lightweight, cost-effective alternative to aluminium, offering good durability for many production runs.
Applications of Vacuum Forming
Vacuum forming is found across industries, creating products like:
Automotive Parts: Bumpers, floor mats, and interior trims.
Industrial Crates and Containers: Used for machinery parts.
Food Packaging: Egg cartons, fruit containers, and yoghurt pots.
Medical Trays and Parts: Sterile packaging for instruments.
Consumer Goods: Items like children’s toys, home accessories, and decorative items.
Advantages of Vacuum Forming
Affordability: Vacuum forming is budget-friendly, especially for small to medium production runs.
Speed: Moulds are quick to produce, and the process itself is faster than methods like injection moulding.
Flexibility: It’s easy to test and adjust designs without incurring heavy costs, making it perfect for prototyping.
Versatility: Compatible with food-safe and medical-grade plastics, it can be used in diverse applications.
Disadvantages of Vacuum Forming
Limited Complexity: Ideal for simpler shapes; intricate parts may need secondary processing.
Uneven Wall Thickness: Thinner materials may stretch unevenly, leading to inconsistent thickness.
Not Cost-Effective for Large Runs: For very high production volumes, injection moulding or other methods may offer better cost efficiency.
Conclusion
Vacuum forming is an accessible, adaptable manufacturing process with applications across automotive, industrial, food packaging, and consumer goods. It’s ideal for companies that need to produce prototypes or small to medium product runs without high costs.
If you’re looking to source a vacuum forming company for your project, PlastikCity offers a simple way to compare quotes from trusted vacuum formers across the UK and Ireland. All the vacuum forming companies have been vetted to ensure they provide high-quality service. Request a quote today to get comparative quotes for your upcoming project.
For more information on What is Vacuum Forming? A Complete Guide talk to PlastikCity Ltd