
Sign In
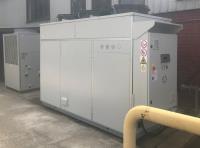
Plastics Company Ipswich
The company has recently acquired a production hall that comprised 17 different machines, dealing with a variety of materials.
The cooling water was provided through two independent circuits.
- The circuit to cool the moulds by a standard industrial chiller and
- The circuit to cool the hydraulic oil fed from a open water tank and an airblast cooler.
The chiller was old and finally broke down and was not viable to repair. The airblast cooler was also struggling to cope and provide enough cooling during the summer through the high ambient temperatures, this was leading to moulding machines needing to run at a slower rate to ensure they did not overheat.
To solve the immediate problem, Refcool supplied a rental chiller and maintained the existing design.
Refcool then undertook a detailed survey of the cooling requirement for each circuit.
A proposal was put together using a single chiller that had
Two independent refrigeration circuits to offer redundancy
Free cooling coil to take advantage of lower winter ambient temperatures
Capacity control allowing more efficient operation at part load.
A heat exchanger to join both circuits together while allowing them to operate at different temperatures.
Looking to achieve a more carbon efficient solution consideration was given to
Electricity usage which would fall by 33%, equivalent to 7,250 tonnes CO2 per annum
Using Propane with a GWP of 3 reduced the Global Warming Potential of the refrigerant gas used to near zero from 41.7tonnes of CO2 equivalent.
For more information on Propane Chiller Installation - Plastics Factory . talk to Refcool Refrigeration Ltd
Enquire Now
List your company on FindTheNeedle.