
Sign In
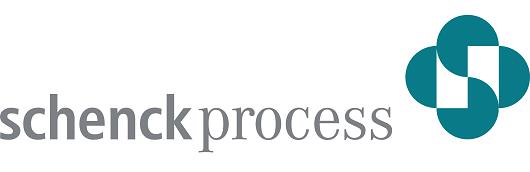
Longevity of Material Storage Solution from Schenck Process Proven in Demanding Circumstances
Storing and safely handling bulk materials such as grain in harbors is a challenging prospect and an area where Schenck Process engineers and supplies a unique solution in the form of its MaxiStore®.
Solving Storage Challenges in Demanding Environment
A customer, part of the dry bulk commodities industry, wanted a long-term bulk material storage solution within their limited available space at a harbor. They contacted Schenck Process for a solution that led to the MaxiStore demonstrating its longevity and starting a relationship lasting over 15 years.
With restricted space within the port, the customer needed to maximize what was available. A traditional loading system uses a high-level conveyor with a tripper supported from the apex of the building roof. Potentially, it could have made for a costly build and resulted in inefficient material loading. Also, controlling the material positioning across the length of the store could have proved difficult for that system.
After establishing that the traditional system wouldn’t solve the customer’s challenges and a more innovative approach was required, the team at Schenck Process proposed the unique MaxiStore system. Based on the combined advantages of proven Redler, en-masse conveyor technology, and an industry-leading approach to the process of store loading, the MaxiStore system used a cranked en-masse chain conveyor within a steel structure to span the building laterally. The machine could move along the length of the store with material fed through the chain conveyor to drop to the floor. It allowed the material to easily be fed to any required storage bay while having the capacity to fill up to the ceiling and along the entire length of the building, optimizing storage volumes for any given space. MaxiStore manages the area safely by minimizing dust that can lead to explosions.
MaxiStore: Durable and Fully Adaptable Solution to Customer Needs
Each MaxiStore system can be specifically designed to meet the customer’s exact needs, no matter how complex. By working with the customer to understand their particular requirements, Schenck Process developed a robust system that optimized the storage volume for their limited store size and maximized profit. The result empowered them to work within their conditions and have a storage system that could operate continuously.
The MaxiStore system is made to handle large quantities of animal feed, minerals, and other bulk materials at rates up to 1,000 tonnes per hour. It enables the user to maximize their space while providing better and safer material distribution. The MaxiStore was proven to provide the most efficient and flexible filling of dry bulk solid materials throughout a storage building.
Schenck Process offers installation and after-sales support—across the entire lifecycle of their process solutions—assuring the customer of the longevity of the systems they design, manufacture, and engineer. With over 100 years of experience in mechanical conveying and storage solutions, the customer benefited from access to a wealth of Schenck Process’s expertise. Maintaining the infrastructure within the harsh marine environment of the port has been crucial to extending the service life of their acquisition, giving them confidence that they had purchased a best-in-industry storage solution.
Having a long-term satisfied customer is a testament to the performance of Schenck Process’s solutions and demonstrates their commitment to developing innovative and efficient automated bulk storage solutions. The system they installed 15 years ago is still working 24 hours a day and remains a fundamental part of the customer’s port operation.
For more information on Complex System Showcases Adaptability in a Highly Challenging Environment talk to Schenck Process UK Ltd
Enquire Now
More News
List your company on FindTheNeedle.