
Sign In
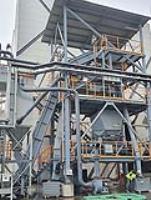
Reaching for Net-Zero with Comprehensive Feeder Technology Package
Schenck Process was approached by The A TEC Group, working on behalf of LAFARGE Cement Hungary Ltd. LAFARGE was looking to install a new alternative fuel concept at a Királyegyháza cement plant, near Pécs in Hungary. As the global leader in building materials and construction solutions, LAFARGE has the ambition to lead the industry in reducing carbon emissions and moving towards low carbon construction – this is underpinned through a strategy 2025 called “Accelerating Green Growth”.
A TEC Group, an Austrian engineering and technologies company that focuses on improving efficiencies in cement plants, has worked with Schenck Process for around 8 years. For this project, A TEC needed to work with an organisation that they could trust to supply the systems for the main burner line in a timely and efficient manner for their client and meet specific levels of performance. This is why they invited Schenck Process to submit a tender response. The key focus for the A TEC Group and the client LAFARGE, was to deliver a compact, economical and highly sustainable solution.
Compact Solutions for Custom Installation
Owned by LAFARGE, the Királyegyháza cement plant is a plant with state-of-the-art manufacturing equipment and a focus on elevated environmental performance. It has been working with the most modern available technology since 2011 and has become one of the major producers of cement with its solutions for the construction industry. Schenck Process successfully designed and proposed a customized solution that aligned closely with its customer’s goals and objectives.
The large capacity plant is responsible for a substantial amount of the delivery of high-quality cement in Hungary; however, its limited footprint posed some unique challenges. Space was restricted and Schenck Process was conscious of the issues this could raise. Schenck Process’s design support capabilities were, as always, focused on meeting the customers’ needs, no matter how complex.
Quick Fitting Modular Design Delivers on Alternative Fuel Handling Flexibility
Schenck Process supplied and installed an array of integrated equipment, ranging from the Multiflex NG Feeder to the Multicell AF Blow Through Rotary Valve; both of which contribute towards improved handling of alternative fuels, in addition to the following technologies:
• Reception stations EcoDock with agitators
• Chain conveyors MoveMaster C
• Magnetic drum separator (positioned externally)
• Collecting screw conveyor MoveMaster SC
• Pneumatic conveying line
• Double hydraulic unit (positioned externally)
Schenck Process fully engineered its holistic approach to the installation to meet the customer specification.
The supply of the Multiflex NG Feeder has provided a more effective alternative fuel feeding solution. By engineering a modular system with a high degree of accuracy, flexible processing abilities, and high feeding consistency, the Multiflex NG can maintain stable conditions within the rotary kiln. By choosing the Multiflex NG, LAFARGE could also utilize the machinery to turn plastic into energy, removing it from land and sea; thus keeping their focus on high environmental performance at the forefront of their activities.
The inclusion of the Multicell AF Rotary Valve allowed its patented air distribution system to maintain consistent feed rates by aerodynamically blowing through materials. The anti-blocking technology ensured a reduced need for cleaning cycles and will extend the overall operation period, maximizing the capacity of the Királyegyháza cement plant.
For more information on Schenck Process Maximizes Client's Sustainability Performance in Alternative Fuels talk to Schenck Process UK Ltd
Enquire Now
More News
List your company on FindTheNeedle.