
Sign In
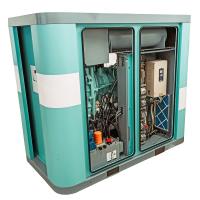
When it comes to dilute and dense phase conveying, designing effective systems that move material more efficiently and safely is at the core of the technology developments at Schenck Process. Thus, the Group has entered an exciting partnership with Lontra to use its LP2 blower that features its innovative Blade Compressor® technology. Schenck Process will be using the blower in conjunction with its Enhanced Dilute Phase Pneumatic Conveying (EDIP) system for trials and customer testing at its Test & Innovation Center in Doncaster, UK. The facility has also installed its patented E-Finity® technology – an exciting prospect for users of dense phase conveyors, particularly in the chemical, food, and pet food industries.
The E-Finity System Revolutionizes Conveying
Dense phase conveying is an energy-efficient method of transporting abrasive or fragile materials through pipelines at very low and stable velocities to minimize product degradation and equipment wear. The airflow allows the material to build on the bottom of the pipe to form a slug. Porous product will allow air through the build-up to convey at low velocities.
This method is particularly well suited for food, pet food, and chemical products. Traditional methods use compressed air supplied at a higher pressure in conjunction with a pressure vessel to discharge the material into the pipeline. In comparison, continuous dense phase systems use low-pressure components such as blowers and rotary valves. However, it is less common due to the unstable nature of air leakage through the valve caused by increased pressure in the pipeline. This leads to critical failure and line blockages.
The Schenck Process E-Finity system overcomes these issues. The patented continuous dense phase conveying system provides gentle and energy-efficient conveying of granular and pelleted products. It controls the air volume and velocity traveling down the pipe. Precise pressure monitoring dictates how the control valve manages the airflow through the pipeline, compensating for any leakage or changes in temperature. It allows the pressured air to be consistent and appropriate to convey the material. Continuous calculations take in a myriad of factors to ensure optimal efficiency.
Optimizing Conveying Performance with EDIP
Dilute phase pneumatic conveying works through the suspension of materials and transporting the elevated particles using air or another gas. The product enters the pipe with a moving air stream that operates at high velocity and low pressure. This system is ideally suited for non-friable and non-abrasive materials and can convey a wide range of sizes, shapes, and densities. Generally, these systems have lower capital costs and are often supplied as component parts. As a result, many systems are overdesigned and suffer from suboptimal performance.
Schenck Process developed its EDIP controller to augment dilute phase pneumatic conveying performance by minimizing the speed of the blower under all operating conditions. Typically, the dilute phase will consider the max-speed condition for the blower, such as the highest rate and longest distance, to ensure there is always enough air in the pipeline. However, the EDIP controller can take in information about the system, such as line size and conveying pressure, to set the blower at the ideal speed. The algorithm adjusts for a tangible conveying velocity that the user can program. This optimization delivers energy savings of around 20% with the added benefits of lower material degradation and reduced equipment wear.
A Perfect Match for Energy-Saving Efficiency
Schenck Process can offer unprecedented energy savings for dilute phase conveying, enhancing them through partnering with Lontra. By using the Lontra LP2 blower with the EDIP technology, Schenck Process can demonstrate the most efficient lean phase pneumatic conveying technology, saving 30% on energy compared to traditional methods.
With its Blade Compressor technology, the patented LP2 delivers oil-free air with the highest efficiency and reliability, boasting 34% electricity savings based on independent testing. Using IoT hardware from Beckhoff Automation and a high-efficiency variable speed drive (VSD) from its partner Yaskawa, the LP2 maintains optimal performance over various speeds with its permanent magnet technology.
Power Combo Boosts Test Center Capabilities
The Schenck Process Test & Innovation Center in Doncaster will use the combined system to test conveying distances of up to 250m on 100 mm and 125 mm pipes at rates of up to 15 tonnes per hour. Customers will be able to test their materials to demonstrate the potential of this energy-saving technology for their specific process. Testing will feature comparisons on parameters, such as feed rate, loss in weight at the hopper, pressure monitoring, and measuring power consumption.
Schenck Process has further plans to develop other technologies for reducing dilute phase conveying energy consumption. The Schenck Process Test & Innovation Center at Doncaster, UK, is a center of excellence for the E-Finity and EDIP technology and is set up to demonstrate to customers how they can optimize their conveying parameters and systems to reduce their energy consumption. Involvement from the customer can be through remote digital technologies like our Digital Twin or even via a direct visit if they wish to participate.
For more information on Technological Advancements in Conveying Technology: E-Finity and EDIP talk to Schenck Process UK Ltd
Enquire Now
More News
List your company on FindTheNeedle.