
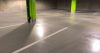
Liquid waterproofing is a durable solution for car parks, but the longevity of finish depends on proper preparation. If the substrate is not assessed and prepared correctly, issues may arise later, with potential liabilities down the line. Here, we guide on pre and post-installation care to ensure a high-quality finish that meets warranty requirements.
What is liquid waterproofing?
Liquid waterproofing is a dual-component resin composed of polymethyl methacrylate (PMMA) that’s flame-free, cold-applied and versatile. In the Soprema range it’s known as ALSAN PMMA and is not solely for waterproofing purposes but also a trafficable surface sealer and finish coat.
When to use liquid waterproofing systems?
The ALSAN system is ideal for sites where flame-based methods are prohibited, weight limitations prevent additional layers or space for equipment is restricted. Its quick application allows areas to be used directly without requiring additional slabs or paving, making it suitable for the refurbishment of car parks that have to remain open.
A full liquid waterproofing system, like ALSAN 700 and ALSAN 870 RS, quartz sand and a finish coat, would generally only be required for top decks or rooftop areas and not necessarily on the intermediate decks. Unless there is a requirement to integrate car washing valet services, in which case it would prevent water damage.
It can also be specified depending on performance requirements, such as slip resistance, structural protection and aesthetics like line markings. It is often used alongside bituminous systems. We offer guidance on the system build-up for a surfacing project.
Avoiding car park surfacing mistakes
This is especially the case in car park resurfacing projects. A recent Soprema survey of a council-owned car park highlighted some issues on the top deck where the asphalt had rippled due to heat and heavy traffic.
The client suggested applying a new product over the existing surface, but this is not recommended. Any underlying damage must be addressed first. Soprema advised the removal of the damaged asphalt and repair of structural issues in a thorough report.
Test to achieve a consistent finish
With the right specification and scope of work in place, contractors must ensure surface consistency during application. Technical data sheets outline important parameters like substrate and ambient temperature. Ignoring these can result in improper curing – either too fast or too slow. To achieve a proper bond, pull-off bond tests must be performed on the deck before installation.
Additionally, the consumption rate for the application of the product also needs to be consistent as it varies depending on the substrate.
Carefully considered installation
Weather plays a crucial role in the application process too. In summer, contractors should work during cooler hours to avoid heat-related curing issues. Similarly, rainy conditions must be avoided for proper adhesion.
Flexibility in scheduling helps to ensure applications proceed smoothly. PMMA is easy to apply across a range of temperatures and humidity. And, with the benefit of no critical overcoating time, it can be applied systematically to suit the schedule with minimum downtime and rapid turnaround.
How to ensure longevity
Once the work is complete and a warranty awarded, ongoing care is essential. Car parks are high-traffic environments, and damage is inevitable. Regular inspections and maintenance help to identify issues early. Collaboration between the client, contractor and manufacturer is key to ensuring warranties remain valid and car park surfaces last for years to come.
For more information on The Key to Car Park Structural Protection and Surface Longevity talk to SOPREMA UK