
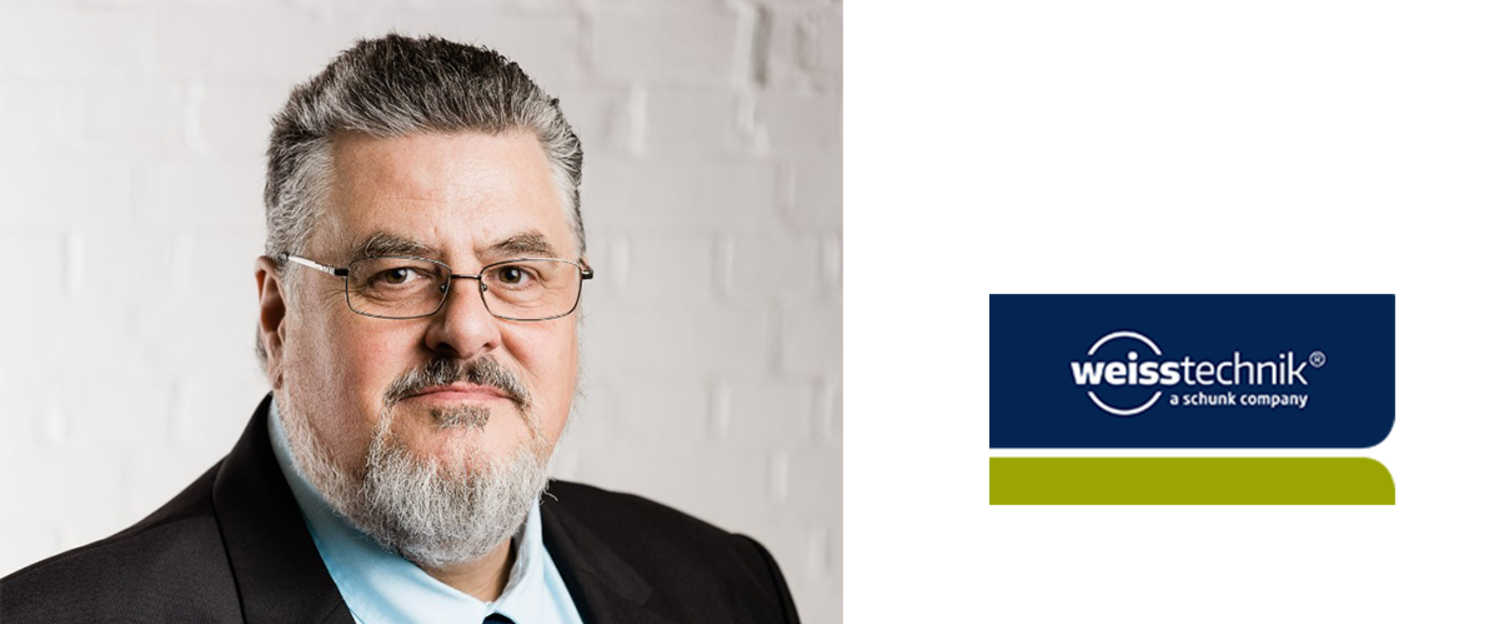
Starting off his career in engineering as a Technical Apprentice in the late 1970’s, Bob Davies has gained a wealth of experience during his 40-year career, having first worked in chemical and process industry with Simon-Carves, the nuclear industry, and then environmental solutions after the UK water authorities became privatised in 1989. After this, Bob moved into cleanrooms, clean environments and specialist industrial facilities; all of which required cleanroom technology to maintain controlled environments that are free of airborne particles, such as dust and microbes, to prevent product contamination and ensure product quality. Through this period, he has accomplished a few degrees along the way and advanced his qualifications, which have been put to good use. Fast forward to current times, and Bob has gained a vast amount of knowledge and experience in developing and providing cleanroom solutions having followed its advancements over the last few decades.
In 2021, Weiss Technik UK brought Bob on board as Business Development Manager to help facilitate the expansion of its cleanroom and controlled environment services in the UK.
Weiss Technik UK, part of the Schunk Group, specialises in providing a wide range of environmental test chambers, air-conditioning technology and cleanroom solutions. Bob works with Weiss Technik’s clients to provide a complete consultancy, design, manufacturing and installation service. His expert knowledge, along with other members of the team, helps clients across various sectors who require cleanroom technology to navigate through the numerous legal regulations and guidelines.
Having worked in the cleanroom sector for over 35 years, Bob has project managed full turn-key solutions for a range of industrial and pharmaceutical clients, including GSK, AstraZeneca, the NHS, LG, and Hyundai (to name a few). Alongside managing projects in a multitude of markets throughout the UK and Europe, Bob has also successfully delivered technologically focussed projects from start to finish – from concept designs right through to construction and installation.
Highlights in his career have included:
i) Securing a £210m project within the semiconductor market by re-establishing a new business unit from its extremely low ebb; from rebuilding it and re-positioning it. This culminated in re-establishing AMEC in the semiconductor market.
ii) Spearheaded the initial contact, tactical positioning, negotiation, winning and initially managing all activities on an £8m pharmaceutical manufacturing cleanroom within the £35m facility.
iii) Unearthed, positioned, secured and project managed expenditure of £1.8m within the high security MOD facility at Porton Down.
iv) Securing smaller projects with much more highly focused speciality, such as aseptic manufacturing facilities and gene treatment cleanroom areas within the expanded NHS Trust at Salford Royal Hospital; which is now a large university teaching hospital in Pendleton, Manchester.
All these facilities encompassed a form of clean environment which can differ in types; classified to national and international standards or requiring validating by independent inspectors that were at the cutting edge of that market.
Bob has been instrumental in driving cleanroom technology for Weiss Technik UK through providing his valuable insights into the market and building strong relationships with clients. Bob’s passion for the industry and ability to understand the unique needs of each client to provide tailored solutions has made him an invaluable asset to the organisation in the short amount of time he has been there.
Throughout his career, Bob has seen cleanroom requirements evolve over the years and has had to keep up with the ever-changing market. He is constantly striving to stay one step ahead of the developments.
Bob explains, “Over my 35-year career, there has always been the need and drive for new and advanced facilities. The requirements demand clean, bug-free, contaminants-free, cross-contamination-free, electromagnetically isolated, particle-free, electrostatically isolated, cold, warm and many other features within a controlled environment. Today, in the world of battery manufacturing, clean and dry rooms have now become more prominent. Being within Weiss Technik, a German owned technology-based foundation company, allows me to help my clients and meet their needs more directly than in the past. Technology is the key today and, when coupled with knowledge/experience, is an unbeatable combination.”
Why is There Now a Focus on Clean & Dry Rooms?
When manufacturing batteries, lithium and other reactive materials must be managed delicately as their properties are extremely sensitive to moisture, temperature and humidity. Lithium-ion requires a humidity level which is extremely low; typically a -50/-60 dew-point. This is then coupled with the need to have particle-controlled environments to recognised levels, such as ISO8 and ISO 7.
Any contamination or moisture can affect the battery’s development, manufacture, performance and longevity, and can even cause safety hazards such as fires/explosions, leakage or short-circuiting. Plus, when batteries are installed in an electronic device, any contamination can impact the final product’s overall performance. So, it is vital that a clean, dry environment is maintained to minimise any possible contamination and the impact this could have on not only the product, but the reputation of the brand providing the product.
Cleanroom solutions are needed everywhere, Bob explains, “The use of clean and controlled environments are in every walk of life, from the complicated specialist production facilities for traditional industrial settings to hospitals, food, automotive, dentists, doctors, vets, classrooms, universities, plant growing, police, computer workshops, mobile phone production and many more. There aren’t many markets today where the environment is not controlled in some way.”
Cleanroom technology is an essential part of many larger industries, including pharmaceuticals, aerospace, automotive, electronics, life sciences and medical. These industries are some of the most sensitive to contamination, and even small particles or microbes can affect their potency and safety. From stability testing at the development stage, testing the durability of packaging under tensile stress and sterile filling of packaging, Weiss Technik can provide cleanroom solutions to create sterile conditions and protect personnel and products.
For Bob, the Pharmaceutical industry has been one of the primary markets he’s served, having spent many years addressing their particular needs and requirements, including for clients such as GSK, AstraZeneca and Pfizer. Aseptic, sterile, fermentation, formulation and many other pharmaceutical production applications all require this simplest of approaches, “Keeping the PRODUCT from YOU and YOU from the PRODUCT”. Cleanrooms are all about that one simple rule – one which he has applied throughout his career.
Bob has also collaborated with clients from the aerospace industry, who rely on cleanroom technology to help them manufacture highly sensitive aerospace components and equipment, such as engines, avionics, satellites and so on. These components are often exposed to harsh conditions, and Weiss Technik’s cleanroom technology helps to ensure extreme cleanliness is maintained during production. If even a small particle of dust or debris finds its way into a component, it could lead to costly repairs or, worst case scenario, catastrophic failures.
The microelectronics sector also relies heavily upon cleanroom technology, as the use of advanced materials and complex manufacturing processes are susceptible to contamination. Microelectronics involves the production of small-scale electronic components, such as computer chips and circuit boards. These components are incredibly sensitive to contamination from particles such as dust and chemicals, and the presence of even the smallest of particles can reduce their performance, lifespan and even render them useless.
The food industry is also beginning to adopt cleanroom technology - helping to ensure quality control, food safety, production efficiency and regulatory compliance. The production of food and beverages involves various processes, such as fermentation, filtration, and packaging, all of which could potentially lead to contamination from harmful microorganisms that could cause spoilage and health problems for those consuming the items.
Bob’s View of the Future of Cleanroom Technology
“If I look to the future, there are few places and markets where clean and controlled environments are not included as necessary elements, and there are still issues that need addressing. Airborne contaminants of any type or the environmental impact on a product or process will always be a requirement. As the needs and drivers of research and development moves the world forward technologically, biologically, genetically, scientifically, socially and economically - there will always be a need for clean environments. The upcoming markets to watch are Hydrogen, Ceramics, Genetics, Data Storage and, of course, Aerospace development, which is a particular interest of mine.
Weiss Technik are in the enviable position of being a Technology Provider / Partner for some clients; a Product Supplier for some; a Subcontractor for others; the Principle Designer and the Principal Contractor to some of our clients; and a total fixed-price provider of solutions to others.”
For more information on Weiss Technik's Bob Davies: 30 Years in Cleanroom Technology talk to Weiss Technik UK Ltd