
Sign In
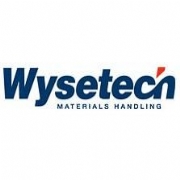
The Aero-Mechanical conveyor uses a wire rope usually ¼” to 3/8” diameter, as the carrier for the discs. The wire rope is usually supplied in 304 S/S, 316 S/S, or galvanized C/S. Plastic coating is also available from some manufacturers on the exterior of the rope. The user should be instructed that a rope assembly definitely has a limited life. On average, the rope assembly will require replacement every 1500 – 3000 hours of operation. Every manufacturer will vary somewhat, but the user should know that the rope has a defined life. During its operation, the rope travels around the sprockets millions of times which results in fatigue of the rope. It is important that the rope be flexible, and strong. Every manufacturer has their own rules and guidelines concerning conveyor length, but remember that the longer the conveyor, the more the rope will stretch and cause the pitches ( length between each disc) to change over its life. On very short conveyors, the rope stretch may not be a consideration, but with the shorter length, the number of cycles around sprocket increases which also causes fatigue. As a general statement, it can be said that the Aero-Mechanical Conveyor is an excellent choice for batch type operations, due to its high capacity and low power consumption. For continuous service the rope replacement factor should be considered. Some items to consider if rope breakage is occurring frequently.
Conveyor run time – Many times the user does not turn off the conveyor after product conveying is complete. It is important that the conveyor be stopped when not in use. The rope assembly will wear as fast when running empty as when running with product.
Starting frequency – If frequent starting and stopping is occurring, a soft-start motor starter is preferred. The soft-start gradually increases the speed of the conveyor when started, instead of the normal motor starter which instantly brings the conveyor up to speed. The soft start puts much less stress on the rope when starting.
Product characteristics – As discussed earlier in this article, cohesive, fatty, or moist products can cause problems. Along with this, larger size particles can be a problem. Most suppliers recommend a maximum particle size to be conveyed be 3/8” – ½” size. It is important to realize that the conveyor has “pinch points’. Areas that larger particle can pinch between the disc and sprocket housing. The larger the particle, the greater the chance of pinching. If the particle is friable, this is not a problem. If the particle is hard, problems may occur. In the area of the pinch point, normally where the discs enter into the convey tubes, the constant interference between these particle and the disc can cause disc wear, or fatigue of the rope due to constant flexing of the rope. Some manufacturers offer various size discs (smaller diameter) which reduce the pinching effect.
Sprocket wear – The sprockets on which the rope engages are normally fabricated of various grades of stainless steel or carbon steel. Abrasion resistant materials are also sometimes used. The Aero-Mechanical conveyor sprocket has guides on each side of the surface on which the discs seat, to assure that the rope assembly stays engaged with the sprocket. Over the life of the conveyor the sprocket edge where the rope rides will wear. For the user that is not familiar with the conveyor, it may be hard to tell. Normally the edge of the sprocket is flat, without groove. When the sprocket edge wears, there will be a groove around the periphery of the rim. Sometimes this groove is so smooth and uniform that it appears to have been machined in the rim by the manufacturer. Keep in mind that as the diameter of the sprocket wears, the engagement of the discs in the sprocket changes and causes the bosses ( front and rear sections of disc ) to wear. Consult the supplier is excessive wear is an issue.
Rope tension - For many current users of Aero-Mechanical Conveyors reading this art
For more information on Most common problem: Rope assemblies breaking prematurely talk to Wysetech Ltd
Enquire Now
List your company on FindTheNeedle.