
Sign In
Problem: Plugged discharge
01-01-2011
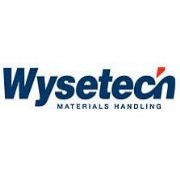
Symptom: Conveyor is stalling, motor burns out, v-belts slip, rope assembly pulls apart, wire rope breaks.
Remedy: Remember that the conveyor runs at 700-800 ft. per minute. The product must be thrown from the discharge by centrifugal force. The most common problem is the discharge of the conveyor not being designed properly. To enable product to discharge easily, the Aero-Mechanical Conveyor manufacturer will typically have a 6” -8” diameter discharge stub. Many times, the mating discharge that is installed by the user is reduced in size, or is at an angle that does not allow product to discharge freely. In general the discharge connection should be kept to the same size as supplied by the conveyor manufacturer and should be situated as close as possible to the receiving vessel with a minimum of discharge duct work. The discharge duct work is often an area where product will build up and ultimately plug.
The equipment at the inlet and discharge of the conveyor should be designed to eliminate the possibility of over-filling the discharge equipment. One of the most common problems occurs when the conveyor is used to fill storage hoppers. Many times there are no safety interlocks in the system to assure that the discharge hopper is not over-filled. Again, remember that product must be discharged by centrifugal force. If product builds up at the conveyor discharge, it will re-circulate product until it finally stalls or breaks the rope assembly. It is best to use interlocks to assure that over-filling does not occur. Normally it is as simple as locating a high level sensor in the discharge hopper, and interlocking it with the convey system so that when high level is sensed the equipment feeding the conveyor stops
For more information on Problem: Plugged discharge talk to Wysetech Ltd
Enquire Now
List your company on FindTheNeedle.