
Sign In
Trouble Shooting Aero-Mechanical Conveyors
28-08-2009
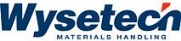
The Aero-Mechanical Conveyor is a versatile system capable of handling a wide range of dry bulk materials. It is rather unique in the method in which it conveys. This type of conveyer is normally not affected by the angle of incline (elevation), and in many cases conveys vertical. Several manufacturers offer 90 degree models. This is to say that the conveyor can convey vertical or horizontal and make one or more 90 degree turns.
Many times the user does not fully understand how the system operates, and how to evaluate the application in which it is being used. This article is intended to give the user a guide in which to trouble shoot their Aero-Mechanical System, or evaluate this system in relation to other types of conveyors. This article will also give a basic understanding of how the system should be applied.
Operation
An Aero-Mechanical Conveyor is a tubular conveyor that has two circular tubes connecting adjoining sprockets. The sprockets are positioned in dust tight housings that provide the proper bearings and seals to support the rope assembly. In appearance, it reminds some users of a conventional Drag Conveyor. That is not the case. The sprocket has equally spaced cavities that seat a disc assembly. The disc assembly is attached to a continuous length of wire rope. The Aero-Mechanical Conveyor concept requires that the discs run at a velocity in the range of 700-800 ft. per minute. This is much greater velocity than a Drag Conveyor, and requires special considerations. The Aero-Mechanical Conveyor should not be confused with the Tubular Drag Conveyor even though the two systems appear to be quite similar.
The conveyor usually has a gravity feed inlet. This inlet may be equipped with a vibrator or fluidization pad should the product being handled require assistance for proper flow. Typically the material would be a powder, and would enter into the inlet sprocket, being taken from the inlet by the velocity of the discs at the lower end of the sprocket. Normally the conveyed product will occupy on average 40% of the volume between each disc. Due to the velocity, the product in most cases will stay in a fluidized state while it is being conveyed. Some products that are cohesive or granular may be an exception to this. The rope and disc assembly conveys the product to the discharge sprocket. The housing that holds the discharge sprocket has an opening that is designed to release product. It is actually the velocity of the particle that enables it to discharge by centrifugal force. In the majority of systems, the discharge opening is 6”-8” diameter. This is rather large taking into consideration that the Aero-Mechanical conveyors will typically use 3” or 4” convey tubes, but is necessary to fully discharge materials.
The concept and operation of the system is rather simple. It is important for the user to keep in mind that the conveyor does not drag the material from inlet to discharge. The conveyor needs to run at a speed to keep material moving at a velocity sufficient to enable discharge by centrifugal force. In general, the easier a product will fluidize, the easier it is to convey by the aero-mechanical method. Products that are cohesive or granular that may not fluidize well may require special considerations.
With the basic understanding of the concept of Aero-Mechanical Conveying, it is easier to understand some of the problems associated with it. Below are some common problems and reasons they occur.
For more information on Trouble Shooting Aero-Mechanical Conveyors talk to Wysetech Ltd
Enquire Now
List your company on FindTheNeedle.