
Material Decontamination for Bilthoven
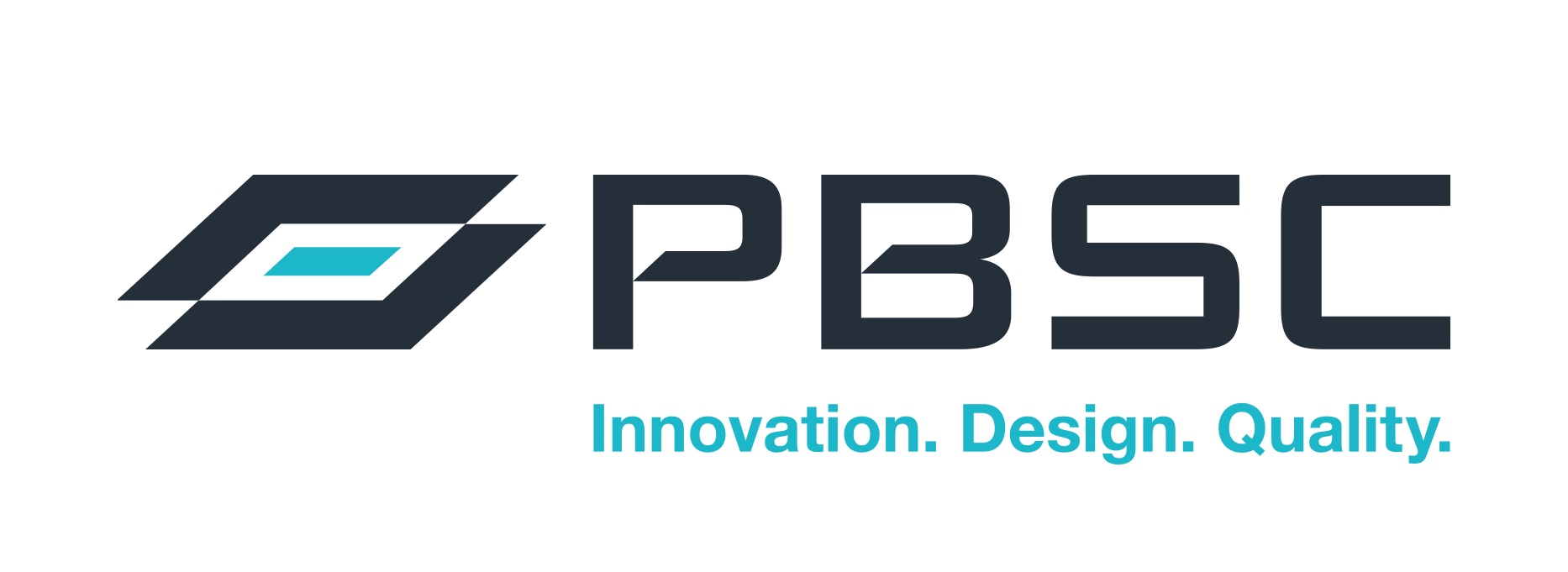
Accommodating bespoke designs to transfer material into Bilthoven Biological’s cleanroom environment Producing
Bilthoven – Producing vaccines to give the world’s population a chance to live their life without disease…
Bilthoven Biologicals is part of the Cyrus Poonawalla Group and produces high-quality vaccines in a state-of-the-art production environment to meet global demand.
Being a bio-engineering and pharmaceutical company that remains at the forefront of vaccine production. Producing Inactivated Polio Vaccines (IPV), Tetanus Vaccines, Diphtheria- Tetanus-Polio Vaccines (DT-PV) and Bacillus Calmette-Guerin (BCG) for the treatment of bladder cancer, supporting the World Health Organisation (WHO) to eradicate Polio.
Spread over 40 acres with an installed manufacturing capacity of over 20 million doses of vaccines annually. The state-of-the-art facility is fully compliant with cGMP and biopharmaceutical
requirements.
PBSC who is the leading manufacturer of cleanroom, high containment, personnel decontamination and material decontamination products around the world, used their expertise to supply the custom designs needed for this project, situated at Bilthoven, The Netherlands.
In association with Tecnilab BMI which offers cutting-edge solutions for safe and efficient production facilities, based in The Netherlands, PBSC contributed with bespoke designs which provided safe and proven solutions.
From Cell to Vaccine…
Products:
Decontamination Hatch
Decontamination Chamber
Solutions & Results
Special additions bespoke for Bilthoven Biologicals:
MAL50 version 2 software decontamination equipment for both Hatch and Chamber, both made from 316L stainless steel.
2 valve air handling systems, with Bilthoven using their HVAC system for air inlet and exhaust for the chamber.
Aeration unit for a reduction of the aeration phase of the HPV cycle.
Actuated pressure pack to enable manual pressure tests.
Gel seals HEPA filter used to be in line with Bilthoven’s site standard.
24v UPS supply integrated into the control panel, used for backup supply to the 24v power components in the event of a power cut.
Win CC software loaded and data networked to Bilthoven’s site server complying with 21 CFR part 11.
Upgrade to gas-tight valves.
Additional bypass fan added to allow for H202 venting during gassing phases of the HPV cycle.
PBSC provided excellent solutions for material transfer into Bilthoven Biological’s cleanroom environment with both the MAL50 Chamber and Hatch designed in a bespoke manner. The Hatch and Chamber allow Bilthoven to demonstrate material transfer using a Bioquell IG-2 Generator and an air-clean cycle.
Vaccines for a better world…
Emma Wolanski – Material Decontamination Project Manager:
“I’m proud the PBSC team were able to deliver a bespoke decontamination solution for such an important global company”
For more information on Material Decontamination for Bilthoven talk to PBSC Limited